Consignment is a form of sales procedure where the products are not initially sold to the consumer. During the consignment process, the vendor delivers the goods to the customer and records the delivery in the consignment stock in SAP. The customer does not pay for any of these goods or services until they use them or sell them. Once the customer initiates a usage or sells the goods, the ownership is transferred from the vendor to the customer, and the customer pays for the goods based on the agreed-upon price.
The stock in these locations is tracked independently using a special stock indicator W. In SAP, the customer consignment location is represented by distinct stock locations within the plant (Customer Consignment Stock). Four different document types are used in the whole SAP consignment cycle. The sections that follow provide explanations of consignment fill-up.
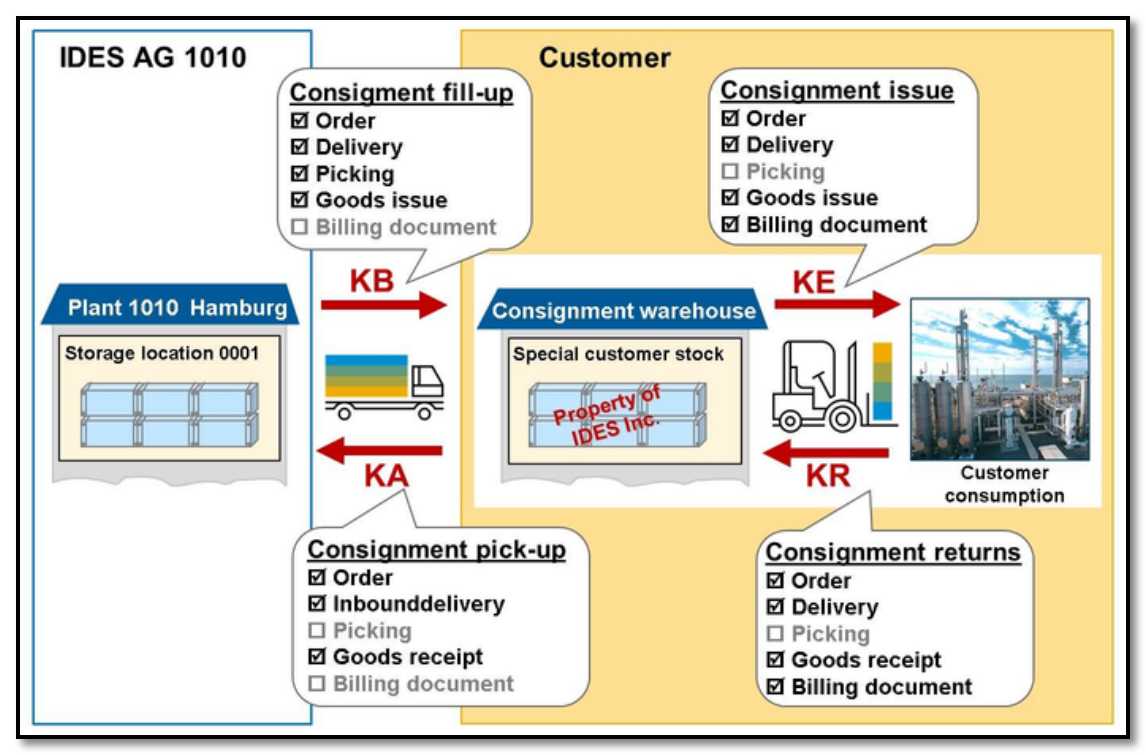
Figure 1 Consignment Process Overview
Consignment Fill-Up
The procedure by which you fill up the stock at the customer's location is known as consignment fill-up. By usage of the transaction code VA01, a consignment fill-up order is created. The document type is KB. The consigned stock is transferred from unrestricted stock to a special stock location when you do the PGI for a delivery for a consignment fill-up order. At this point in the consignment sales cycle, there is no billing to the customer because you still control the stock. There is also no material valuation entry made to accounting because the goods are relocated within the plant from the standard storage location to a customer consigned location
Consignment Fill Up Flow Steps
- Create Consignment Fill Up Order (Tcode VA01)
- Create the delivery for Consignment Fill Up (Tcode VL01N)
- Do the Picking and post Goods Issue (Tcode VL02N)
- Create Consignment Fill Up Order
Step 1:Enter T-code VA01 in the command field. Enter Order type KB and sales area in organizational data.
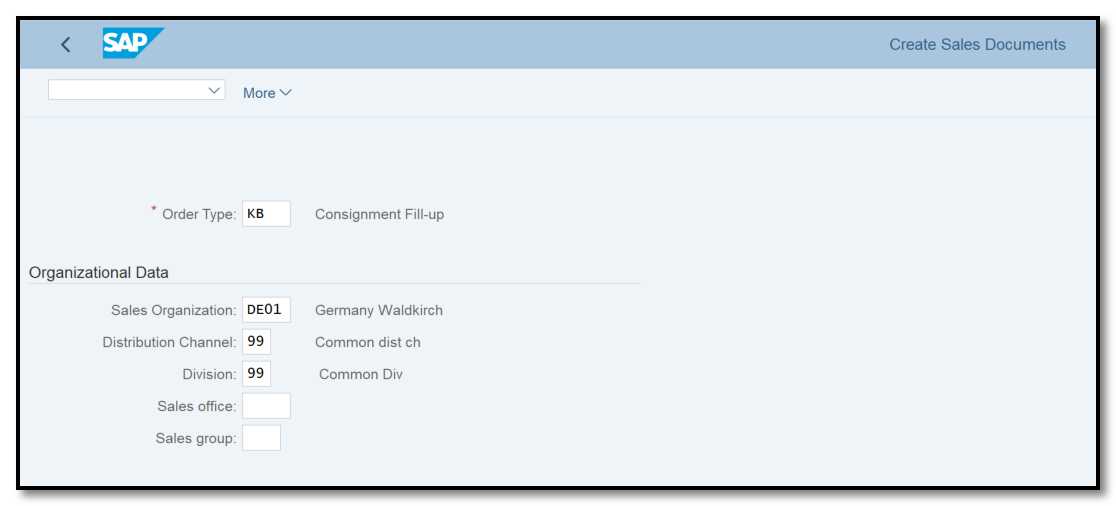
Figure 2 Consignment Fill Up Order Creation: Initial Screen
Step 2:Enter customer ref. and the cust. ref. date. Add the material and quantity, and save it.
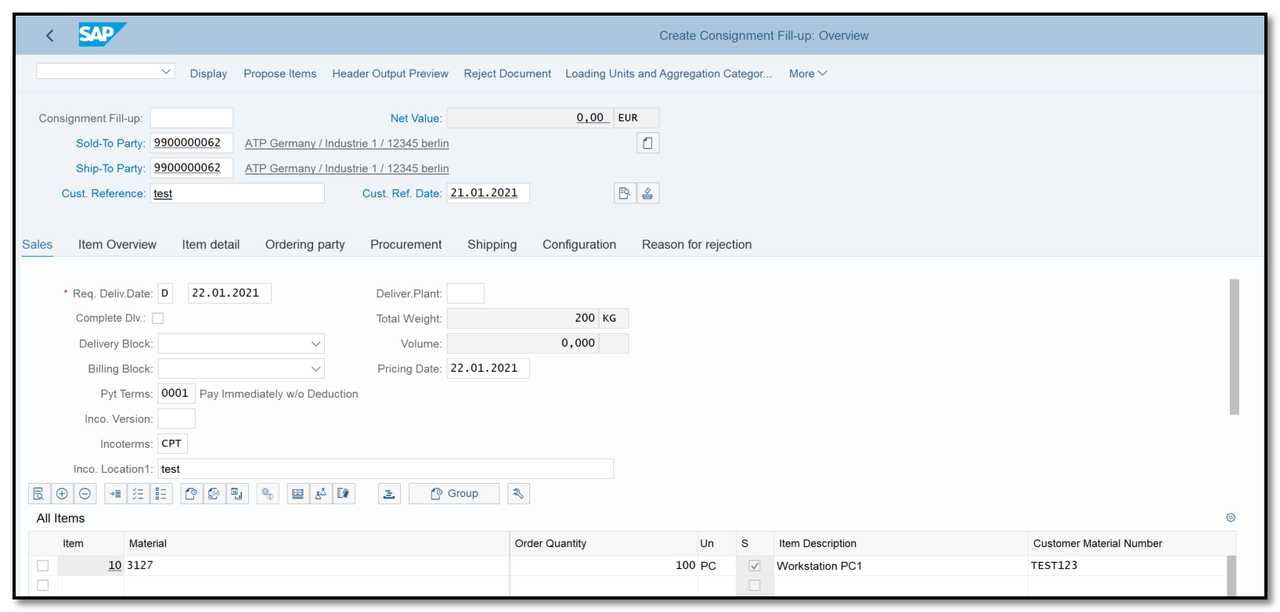
Figure 3 Consignment Fill Up Order Creation: Overview
- Create the delivery for Consignment Fill Up
Step 1: Enter T-code VL01N in the command field. Enter the shipping point and the consignment fill up order number.
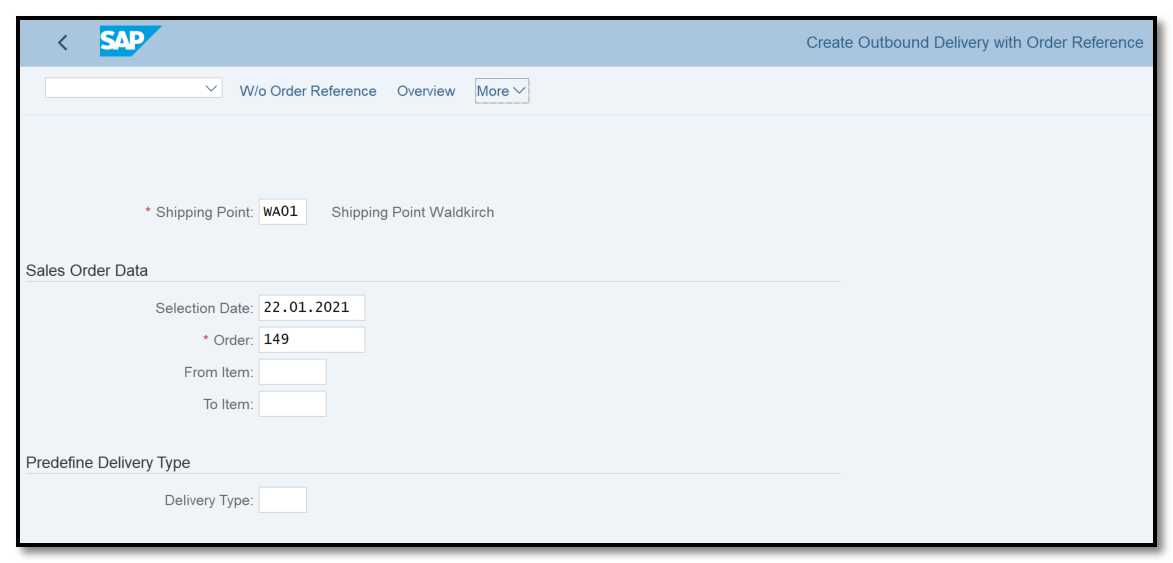
Figure 4 Delivery Creation for Consignment Fill Up: Initial Screen
Step 2: The data will be copied into the delivery
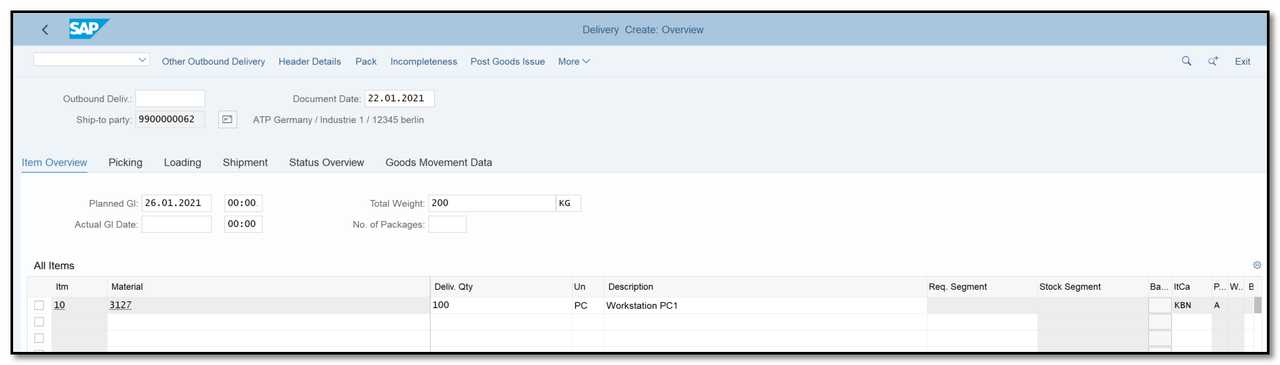
Figure 5 Delivery Creation for Consignment Fill Up: Overview
- Do the Picking and post Goods Issue (Tcode VL02N)
Step 1: Go to transaction VL02N and enter the delivery number. Fill in the picking quantity and click on the "Post Goods Issue" button.
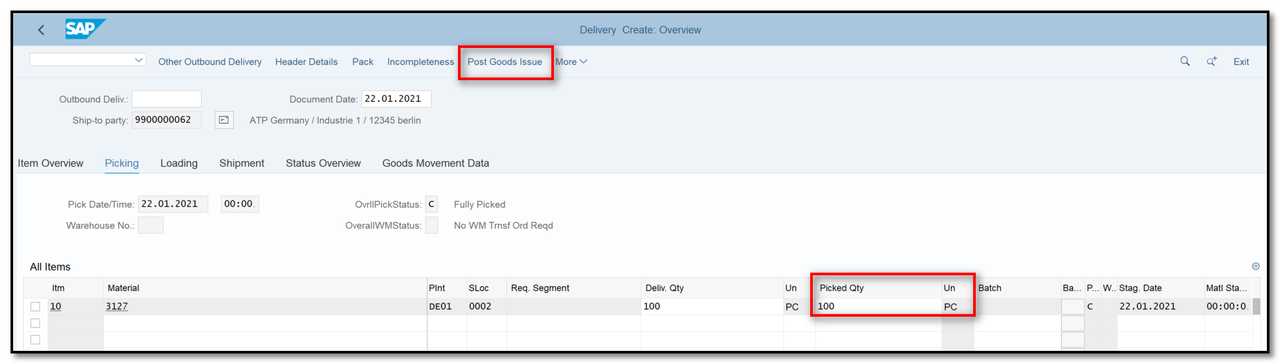
Figure 6 Consignment Fill Up Delivery: Picking, Post Goods Issue
Step 2: To check the status of consignment fill up go to transaction VA03, enter order number and click on Document Flow button.
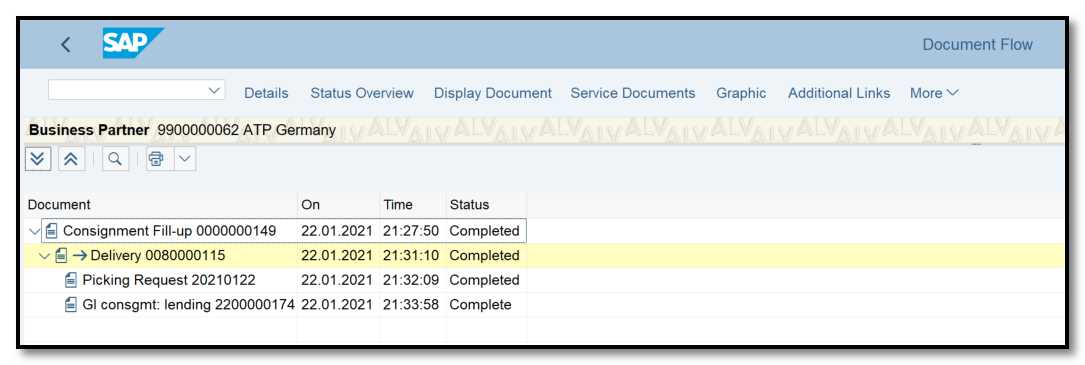
Figure 7 Document Flow – Consignment Fill Up
Step 3: You can also check whether the goods have been moved from their normal storage location to the customer's. Go to transaction MMBE and enter the material number.
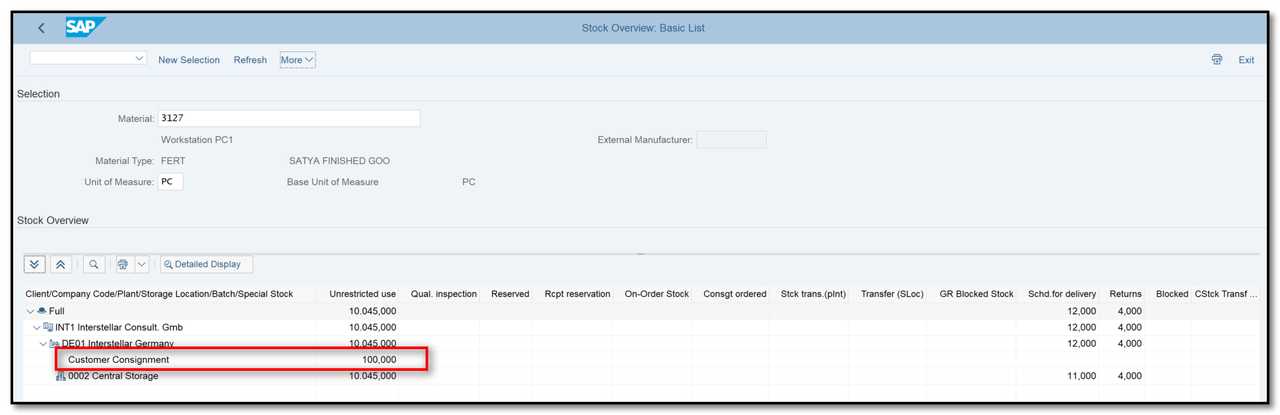
Figure 8 Stock Overview - Consignment Process