Using the transaction code MM01, you can create new material master record or extend existing material master. The menu path is:
SAP Menu ➢ Logistics ➢ Sales and Distribution ➢ Master Data ➢ Products ➢ Material ➢ Other Material ➢ Create
First specify the industry sector and material type that you want to set up on the screen depicted in Figure 1. If you only want to expand existing material, enter material number, industry and material type will be populated automatically.
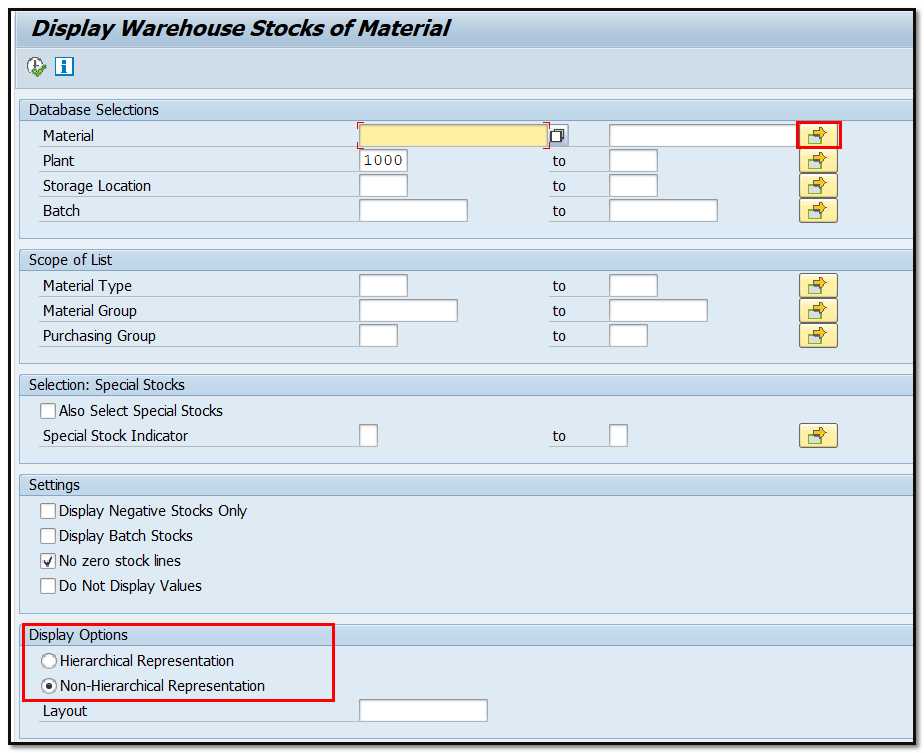
Figure 1 Material Creation – initial view
To use an existing record as a basis for a new product, the Copy From field can be used to select the appropriate source material and organizational level.
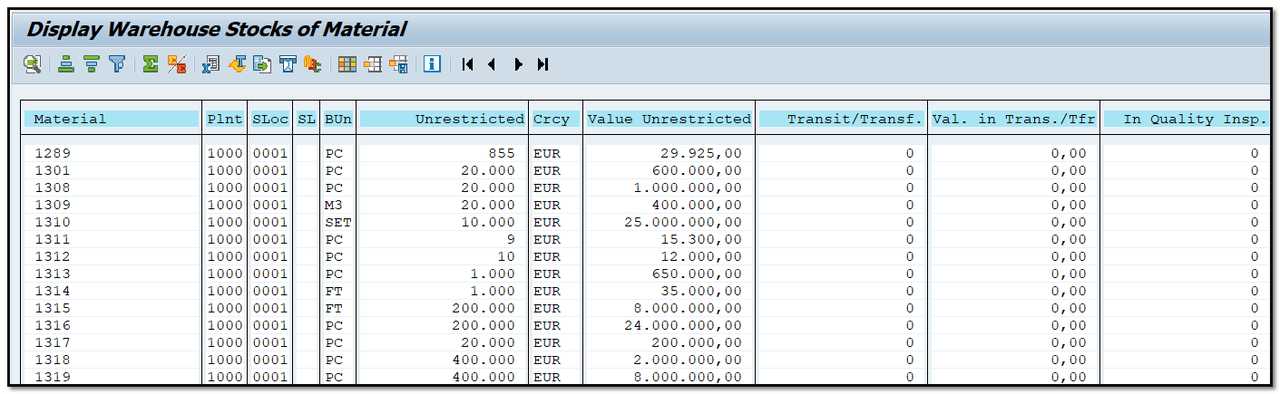
Figure 2 Material Creation - selecting views
To choose which data screens to create, simply click on the Select View(s) button. For the purchasing department, refer to Figure 2 for the recommended views.
Once you select the views and press Enter, another dialog box will appear.
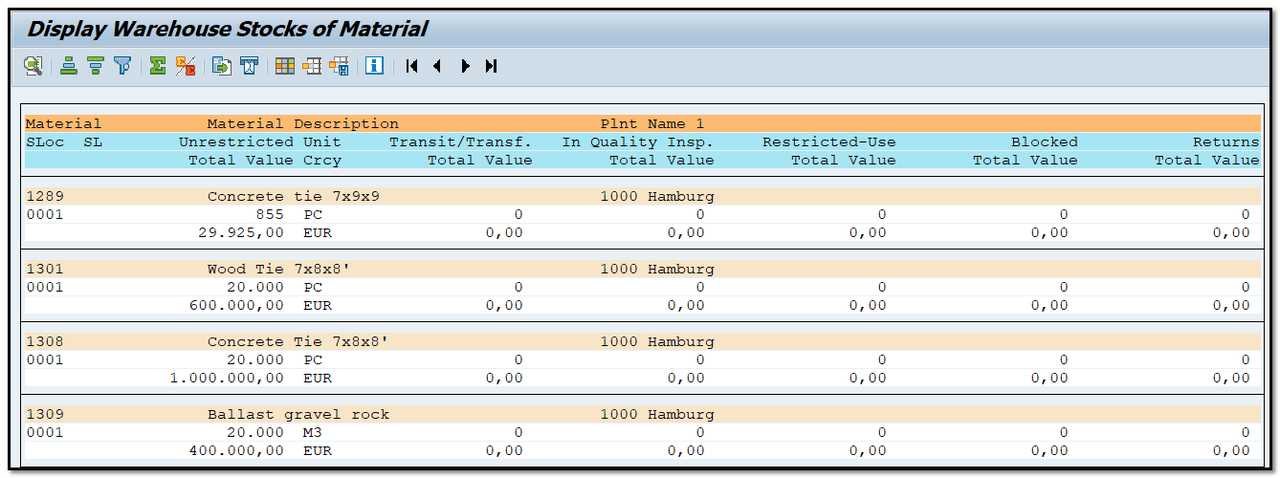
Figure 3 Material Creation – Organizational Levels Selection Window
You must next specify the organizational levels (plant) for which the data will be created based on your choice, then you will get the screens to maintain the data for warehouse and plant data.
Warehouse Management Views
SAP Warehouse Management (WM) views in Material Master data provide an important source for efficient warehouse management. The WM views contain all the master data required to manage a particular warehouse, such as storage bin locations, material movement plans, and stock transfers.
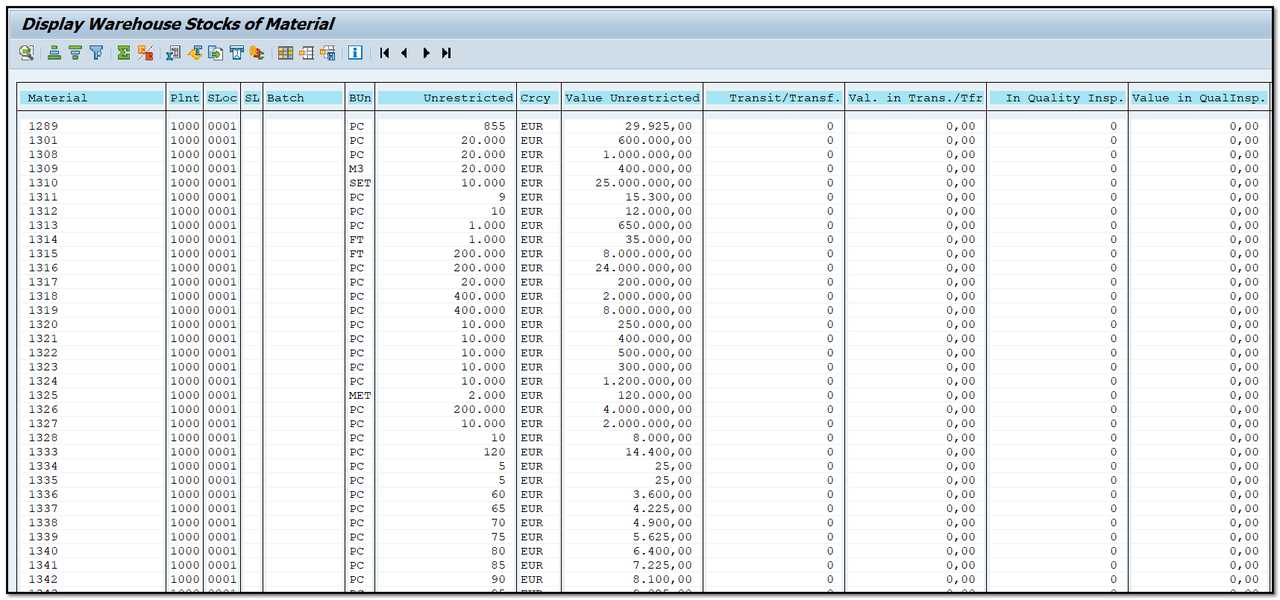
Figure 4 Material Creation – Warehouse Management 1 View
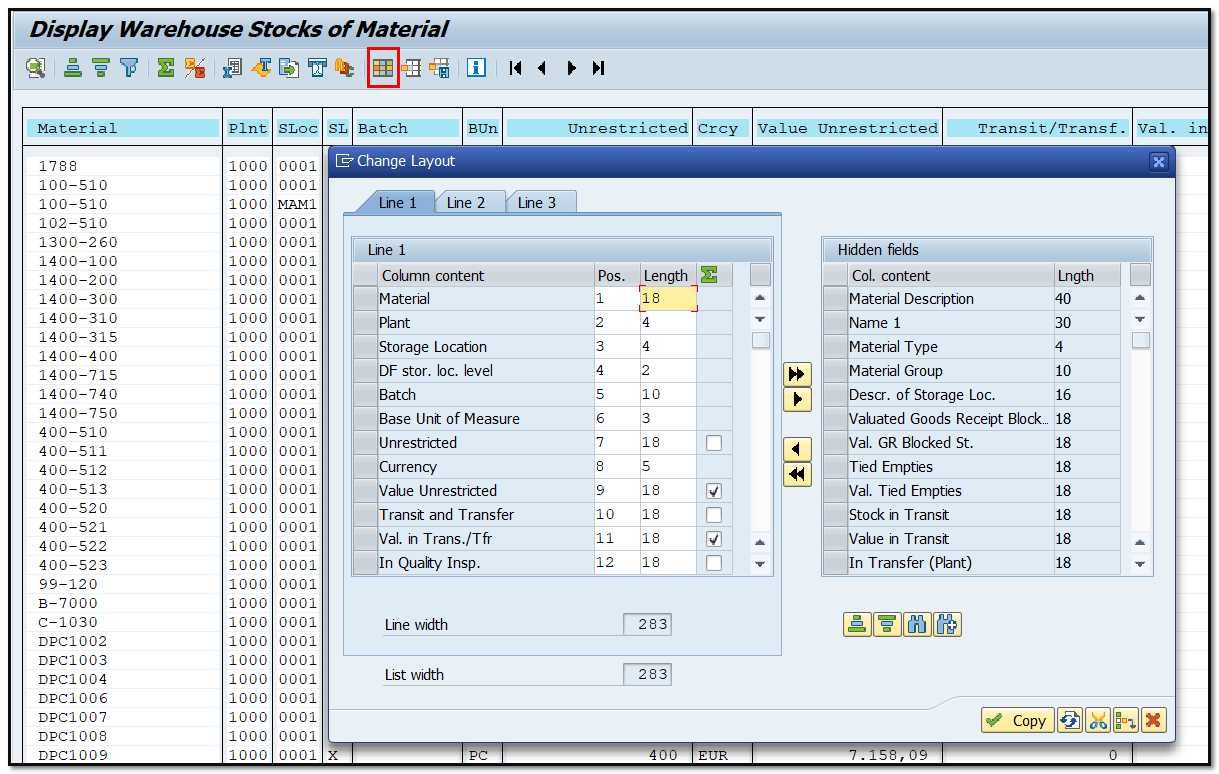
Figure 5 Material Creation – Warehouse Management 2 View
Plant data – Storage 1 View
The data for maintaining this view should come from the warehouse administration team. The majority of them are plant-level storage data.
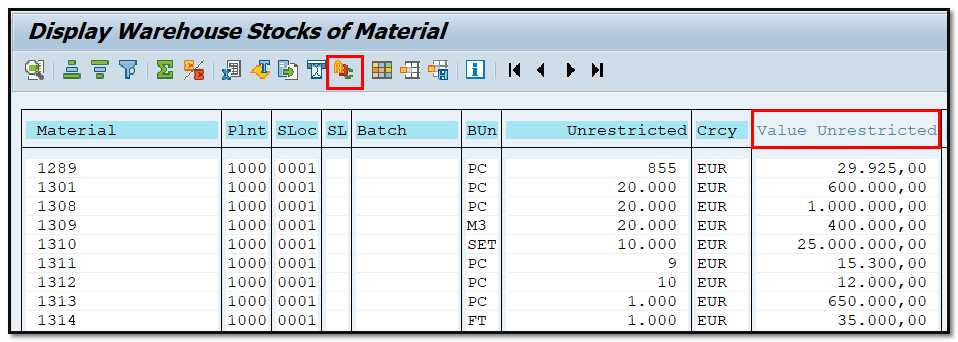
Figure 6 Material Creation – Plant data / Storage 1 View
Unit of issue This is the container into which material is released from any plant storage location (except for the warehouse managed locations which have a setting that overrides this field value).
Storage Bin (1) identifies the storage bin where the material is kept within a storage location. The significance of this storage bin depends on whether or not you employ SAP warehouse management. On goods receipt/issue slips, it can be seen. However, this value serves only as information if the warehouse management system is running.
Temperature conditions (2) the required material storage conditions in terms of temperature.
Storage conditions (3) material-specific storage requirements.
Minimum remaining shelf life (4) Minimum amount of time that must pass before the material can be stored (if the time left is less than the minimum, the system will refuse to accept the products).
Total Shelf Life (5) From the date of manufacturing to the expiration date of the shelf life, this is the total amount of time that the product will be usable. The system assumes that the date entered upon goods receipt is the date of production of the material if the value is entered in the material master record. Then, based on the date of production and the overall shelf life, a shelf life expiry date is determined. The system assumes that the date entered upon goods receipt is the material's shelf life expiration date if there is no value put in the material master record.
If the goods receipt is accepted, the system updates the shelf life expiration date in both the batch master record and the material document.
Plant data – Storage 2 View
These fields were covered in detail in articles for general and sales views (Basic view 1 -Weight/Volume part, Sales - General - General Plant Parameters section).
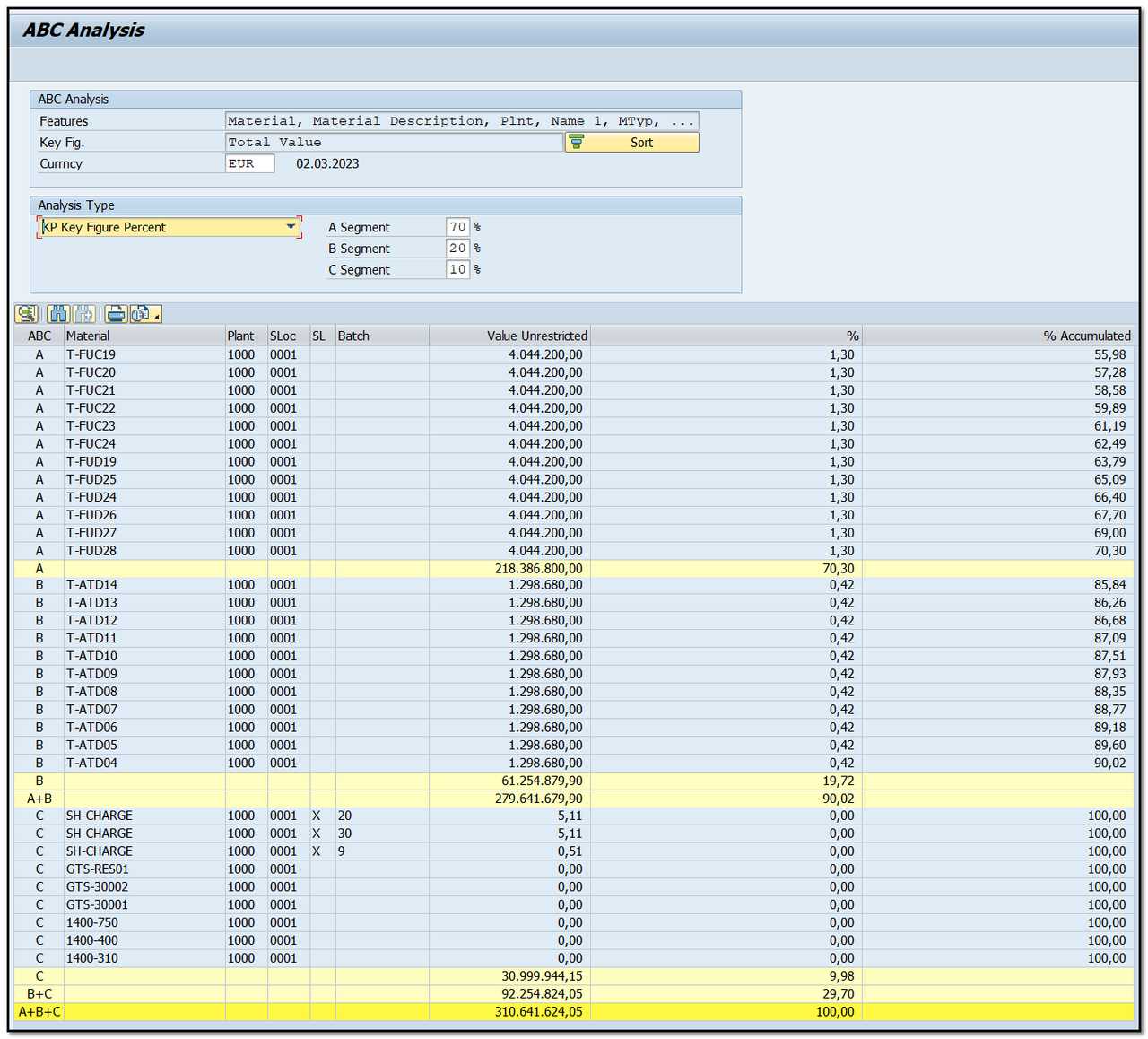
Figure 7 Material Creation – Plant data / Storage 2 View