Using the transaction code MM01, you can create or extend a material master record. The menu path is:
SAP Menu ➢ Logistics ➢ Sales and Distribution ➢ Master Data ➢ Products ➢ Material ➢ Other Material ➢ Create
Please indicate the type of material you plan to use on the screen shown in Figure 1. To identify the industry (Chemical, Pharmaceutical, Retail, and so on) to which the material belongs, use the Industry Sector field. To expand existing material, simply enter the material number and the system will automatically populate the industry and material type.
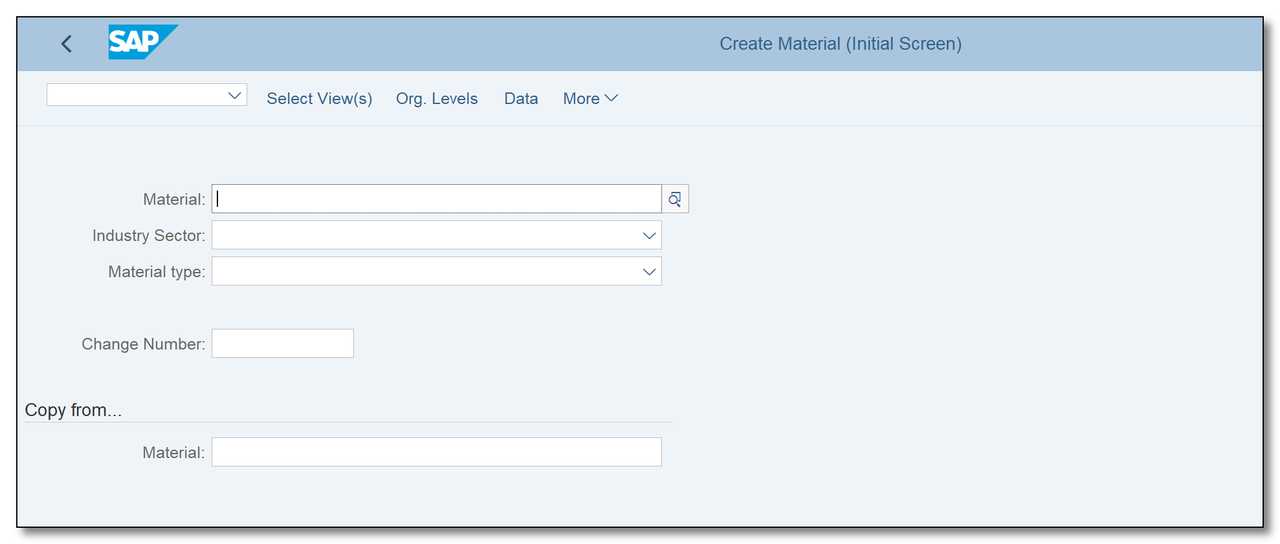
Figure 1 Material Creation – initial view
There is a mechanism to allow you to create a product by copying it from an existing record. To identify the source material and organizational level from which the data can be copied over, use the Copy From field.
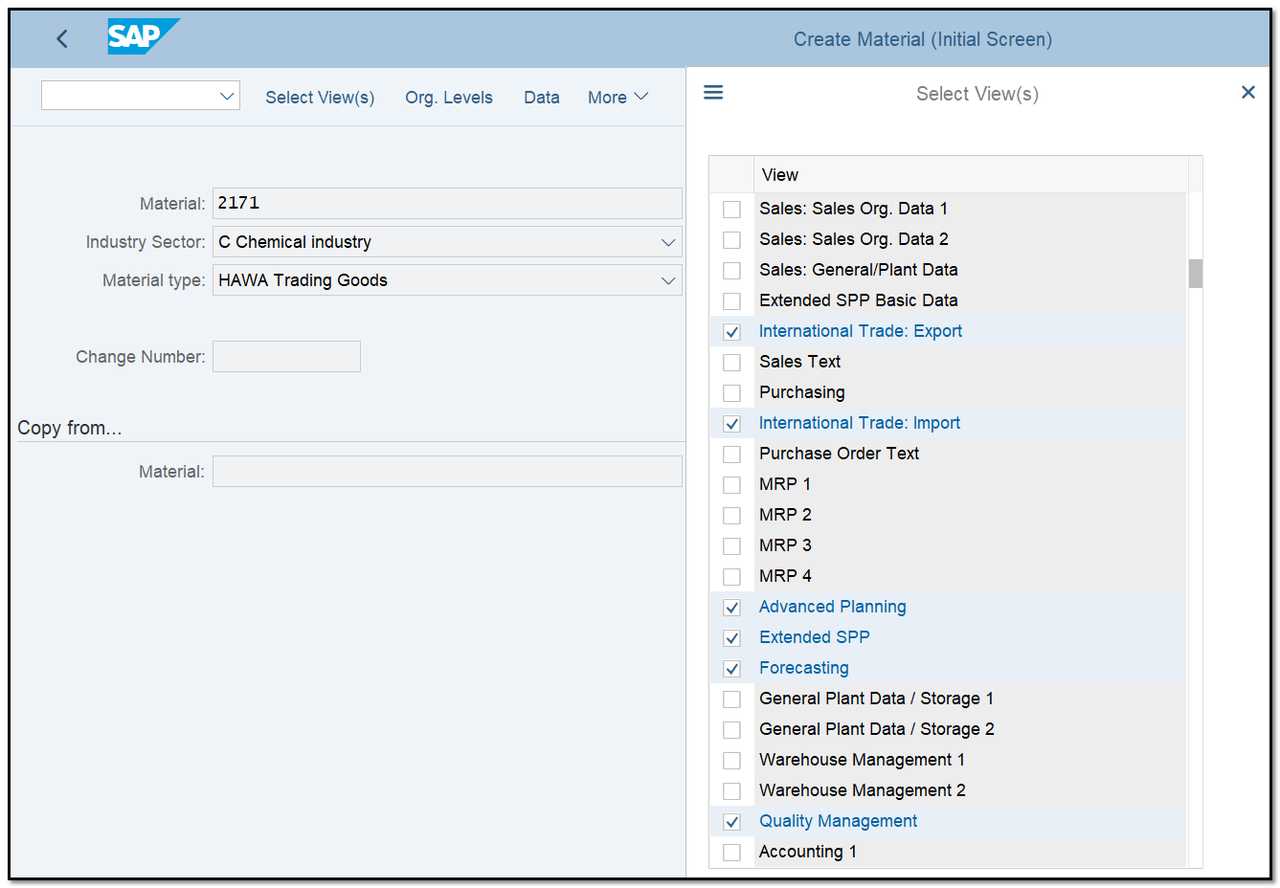
Figure 2 Material Creation - selecting views
You can select which data screens you want to build by clicking the Select View(s) button. For the sales department, choose the views as shown in Figure 2.
Once you select the views and press Enter, another dialog box will appear.
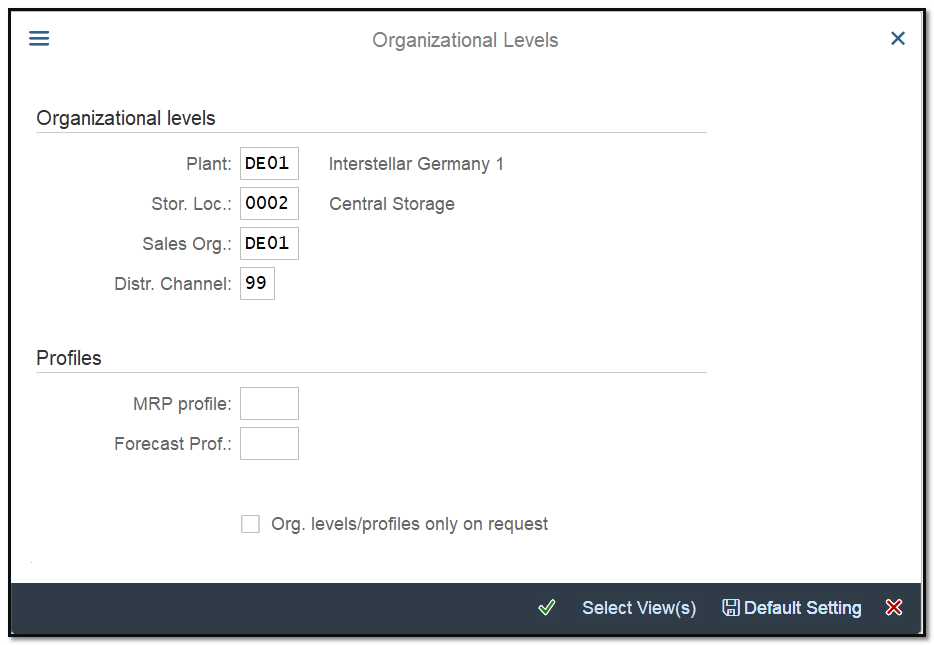
Figure 3 Material Creation – Organizational Levels Selection Window
You must next specify the organizational levels (plants, sales organizations, etc.) for which the data will be created based on your choice.
The SAP system will display all values for the Plant, Storage Locations, Sales Organization, and Distribution Channel where the selected material is already maintained if you either press F4 or the Search button during Change and Display transactions.
After you choose the views and click enter, you will be redirected to the specific views.
Quality Management View
In the Quality Management module, this view is used to set up the materials for quality inspection operations. The information needed to maintain this view must be provided by the administrators of that module.
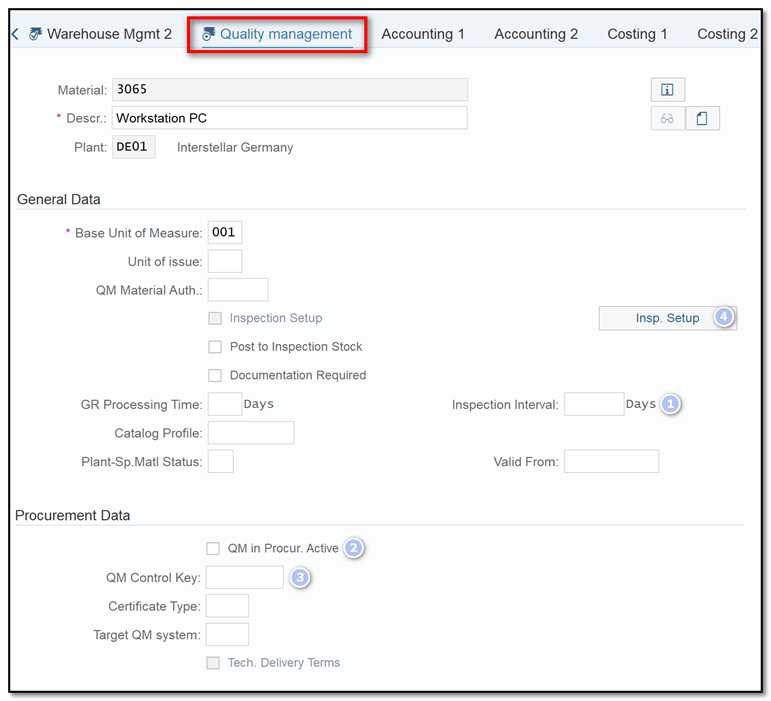
Figure 4 Material Creation – Quality Management View
Inspection interval (in days) (1) period of time between repeated inspections of the same batch.
QM in Procurement active (2) enabling material quality management during the procurement process.
QM control key (3) used to specify requirements for procurement quality inspection. Until the completion of the material inspection, you may establish a delivery block, an invoicing block, and other sorts of blocks. In customizing, the consultant has predefined possible entries.
Inspection setup (4) This shows whether at least one inspection type has been configured. You can select the type of inspection you want to use for this material during setup. Your QM consultant must predefine setup types. Select the appropriate inspection type from the QM team's established options by clicking the Inspection setup button. Then, save your modifications.