Picking is the action of physically gathering the goods for shipping. Either the plant or a warehouse location might be used. A document called a transfer order is used to carry out the picking procedure if the SAP Warehouse Management (WM) module has been implemented.
The Picking Process
When creating or changing delivery transactions, you can reach the picking screen. You can modify the quantity on the picking tab of the delivery document after picking is finished in the warehouse.
The list of all deliveries that are ready for picking is produced by the transaction VL06P. The daily workload can be planned with the use of this list. You generate transfer orders in mass with this transaction when used with WM.
Customization for Picking
When configuring the picking process in SAP, there are a few key parameters that are covered in the sections that follow.
Determining Relevance for Picking
Using the transaction OVLP you can activate picking. The menu path is:
IMG ➢ Logistics Execution ➢ Shipping ➢ Picking ➢ Define Relevant Item Categories
Look at Figure 1 Select the picking-relevant item categories on this screen, then turn on the picking flag.
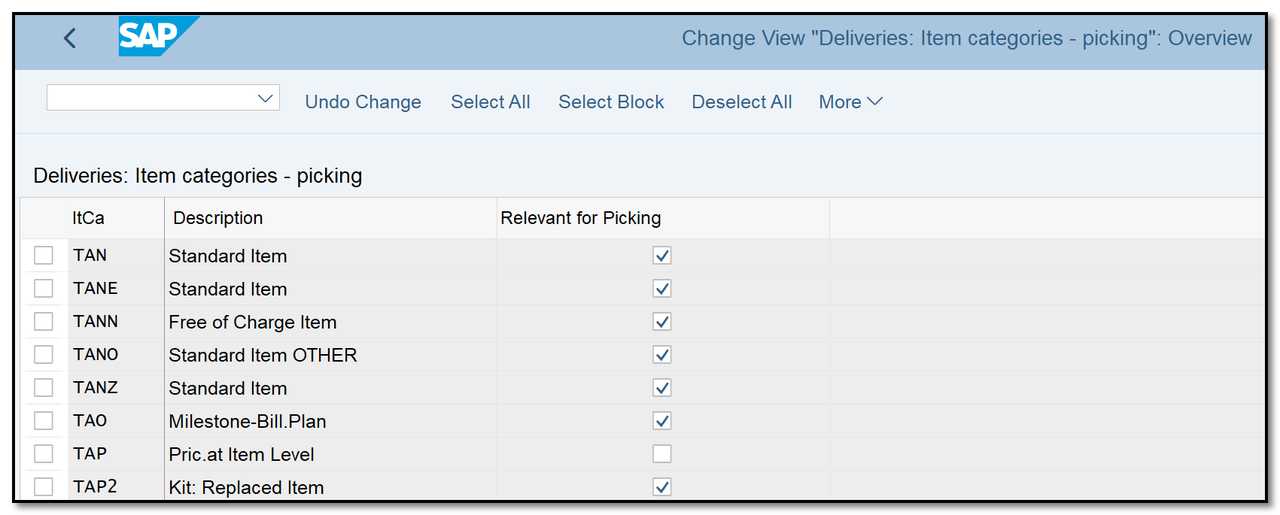
Figure 1 Item categories relevant to picking
Specifying Rules for Picking Location
You must indicate the location from which an item is to be picked up when marking it as appropriate for picking. This is the storage location in SAP. You must consult your WM or MM/IM team to obtain a list of the storage locations where the finished product will be kept in order to make these adjustments.
The delivery can automatically determine the storage locations. For this purpose, SAP (the MM module) comes with two predefined alternatives or rules:
- MALA rule: Based on the plant, the shipping point, and the storage condition, the storage location is chosen.
- RETA rule: Based on the plant, shipping point, and situation, the storage location is chosen.
We'll refer to the MALA rule throughout this session. The menu path in customization is as follows to choose the rule:
IMG ➢ Logistics Execution ➢ Shipping ➢ Picking ➢ Determine Picking Location ➢ Define Rules For Picking Location Determination
You can specify a rule for each delivery type in this setting.
Setting Up Automatic Picking Location Determination
The plant, shipping destination, and storage condition are the variables that define the picking location (storage location).
In the MM module, the plant is the highest organizational level, a physical independent entity. It could be a company's operational unit, production plant, or sales branch.
Shipping point is a location where the goods and services are delivered to the customers. The SAP SD module's shipping point is a separate organizational unit that handles both incoming and outgoing deliveries.
The conditions under which the item is to be stored are indicated by this field, which is kept up to date in the material master. (Refrigeration, for instance, is a unique storage condition.)
To specify the potential storage conditions in customization, the menu path is:
IMG ➢ Logistics Execution ➢ Shipping ➢ Picking ➢ Determine Picking Location ➢ Define Storage Conditions
You can choose a two-digit code for the new storage condition and add a description, as illustrated in Figure 2. There are two unique storage conditions in the our case: 90 and 91. This field can be found in the Plant Data/Stor material master view (see Figure 3).
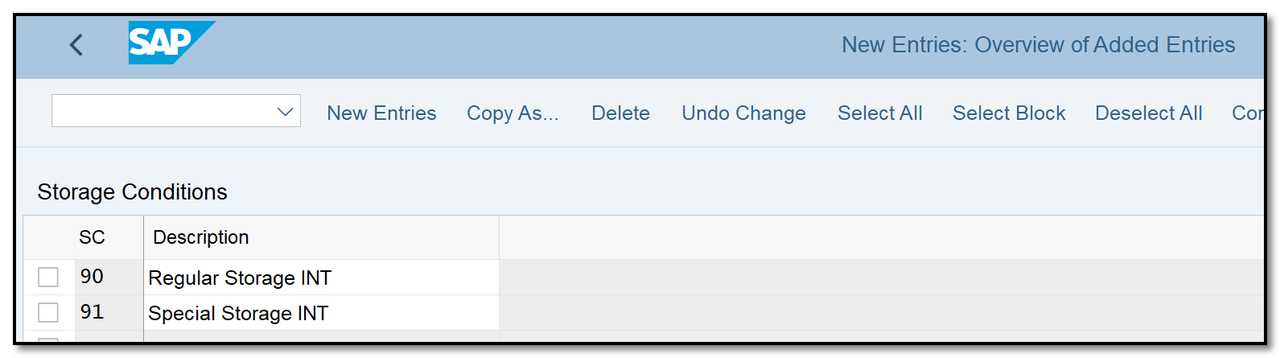
Figure 2 Defining a storage condition
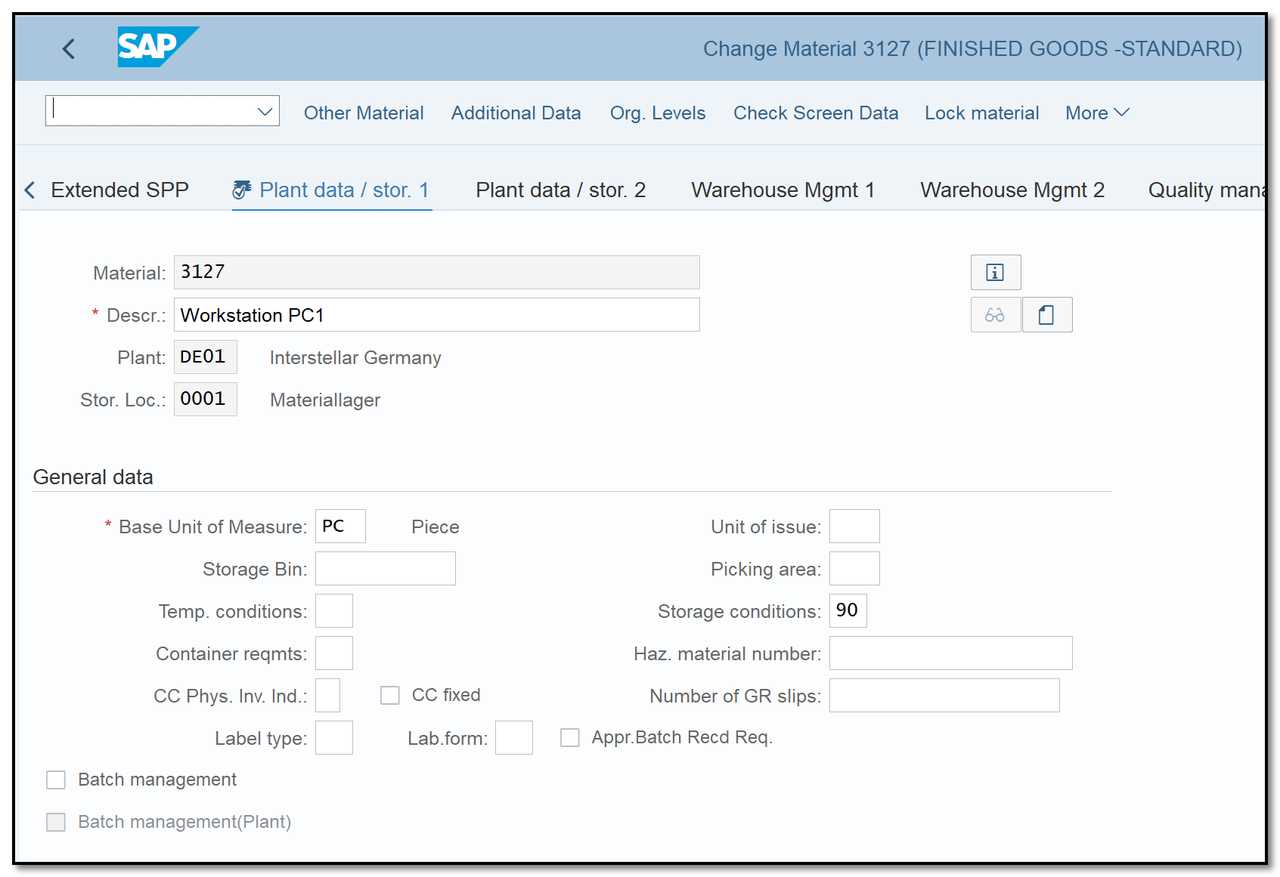
Figure 3 Assigning a storage condition in the material master
The actual determination of storage locations will then be covered.
Follow the menu path:
IMG ➢ Logistics Execution ➢ Shipping ➢ Picking ➢ Determine Picking Location ➢ Assign Picking Location
Then, for each plant, shipping point, and storage condition combination, define the storage location.
We designated a storage location for plant DE01, a shipping point WA01, and each storage condition in Figure 4.
Also take note that we did not define any storage conditions when we added a general record (in the first row). This indicates that the default storage location 0001 will be chosen for materials for which we haven't specified any particular storage conditions based only on plant and shipping point.
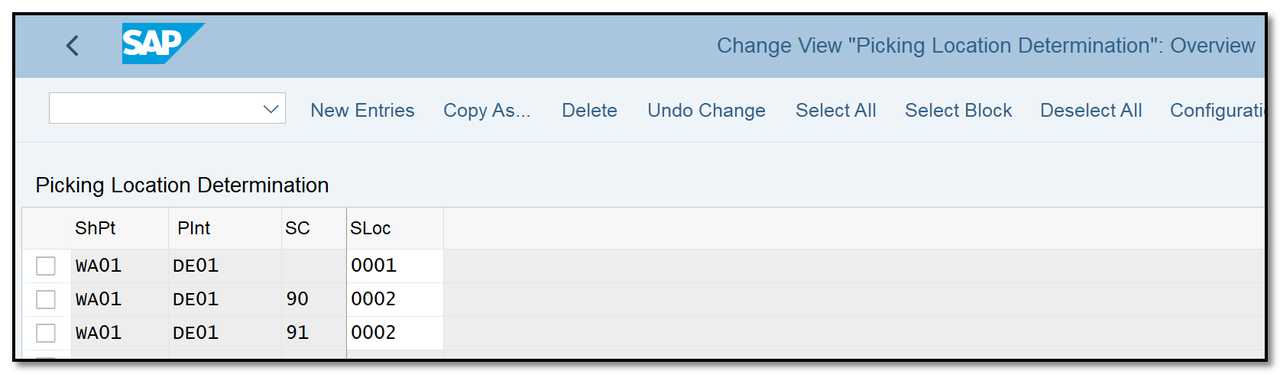
Figure 4 Storage location determination
Picking with Transfer Orders in Warehouse Management
Picking will be done in the SAP Warehouse Management application if warehouse management has been set up for a storage location.
If so, there is a further action to do, which is to create a transfer order (LT03). The picking procedure is thereafter completed in WM. The stock is physically removed from the storage bins in the warehouse in accordance with the instructions in the transfer order. The transfer order is confirmed following the process using transaction LT12.
The delivery document then finalizes the last steps in the logistics execution process.
Wave Picking
Picking runs are scheduled in advance in large warehouses or plants. Deliveries that are scheduled for pick-up at around the same time are combined. The picking team can move around the warehouse and acquire goods for all deliveries at once thanks to a method known as wave picking.
Look at Figure 5 right now. You can run a periodic task to pick up all deliveries that are due for picking within a given time frame using transaction VL06P. The results show that, if WM is enabled, a transfer order for each delivery can be created in waves or batches.
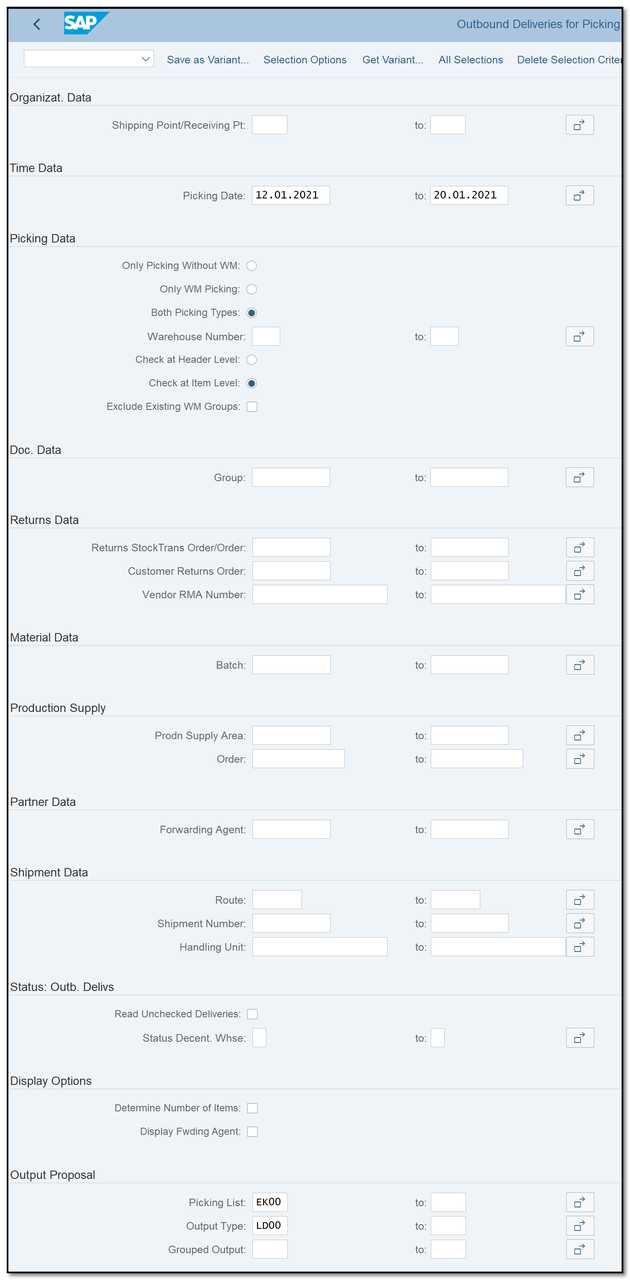
Figure 5 Picking due list