The next step after picking the items is packing them for shipment. The planning and carrying out of this procedure are covered by SAP's packing functionality.
Utilizing distinct material master records, SAP is also set up to handle packaging materials like boxes and crates. A separate material type, VERP, sets these materials apart. You must choose the proper packaging material for the goods being transported when you are packing. Additionally, you can receive customized packaging guidelines from some customers for all shipments going to a particular ship-to address. These elements are subject to your control through customization stages. We'll go into more detail about these steps now.
The Packing Process
Each delivery can be individually packed, or packing stations can use a special transaction.
Packing in Individual Delivery Documents
By choosing the “Pack” button in VL02N on the delivery document, you can access the packaging screen (Figure 1).
The lower pane displays the objects that need to be packed, while the upper window updates as new handling units (HUs) are added.
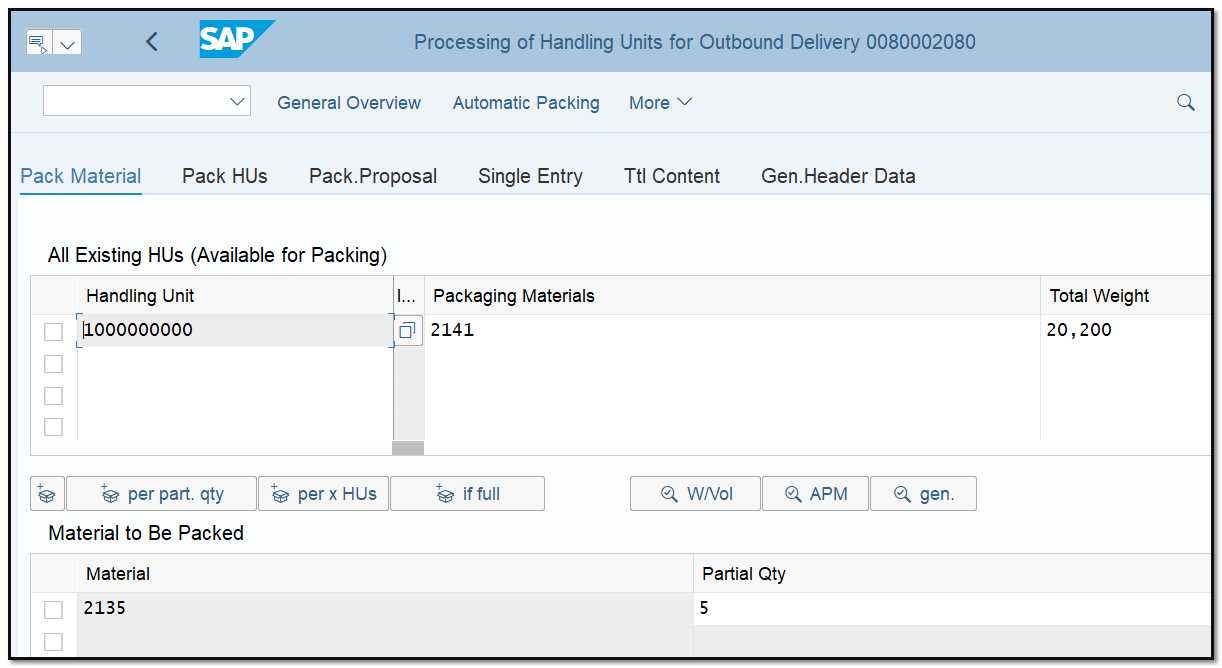
Figure 1 Packing overview screen
You can enter any packing materials on the Pack Material tab and continue to create handling units until all products have been packed.
The handling units can be packaged into higher units using the Pack HUs tab. Using this functionality, you could, for instance, pack many boxes into a crate or several crates into a truck.
The New HU Per X HUs button enables you to pack two cartons (packing material 2141) into a crate (packaging material 2142), as seen in Figure 2.
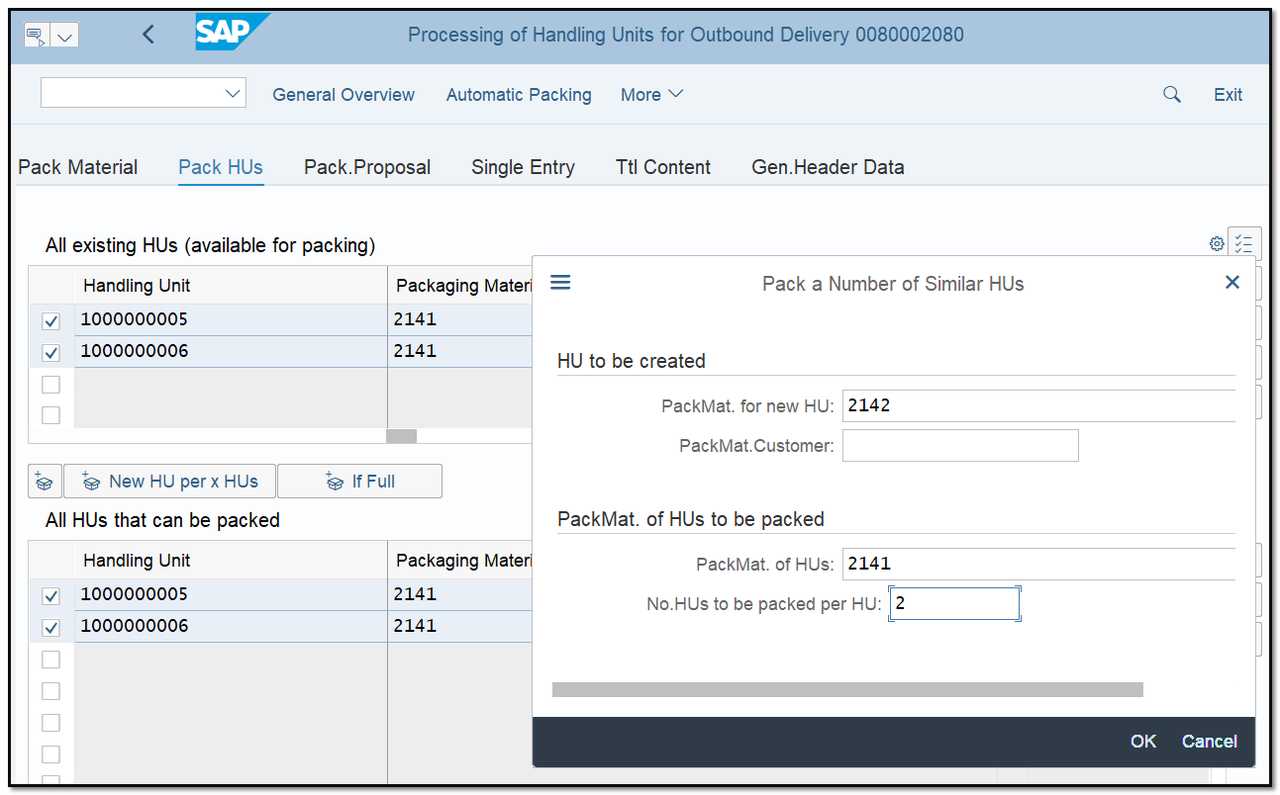
Figure 2 Packing handling units
You can always examine what kind of packaging materials can be utilized to pack the item. For this, follow the menu path
Menu➢ Extras ➢ Allowed Packaging Material.
When you follow that path, a dialog box similar to that in Figure 3 will show up and provide you alternatives for packaging your goods. This makes it simple to narrow down the search and eliminates errors.

Figure 3 Using allowed packaging material to limit options
Packing Stations
We recently went over the packing procedure from a delivery document.
But it is also possible to set up and use a unique packing transaction code that is intended for packing stations, which are particular places in the factory or warehouse where packing is being done.
Follow the menu path to get to the packing station transaction:
SAP Menu ➢ Logistics Execution ➢ Outbound Process ➢ Goods Issue For Outbound Delivery ➢ Pack ➢ Packing Station (transaction HUPAST).
Press Enter after entering the packing station. A complete packing cockpit window, as seen in Figure 4, opens, allowing you to pack materials into HUs and then pack the HUs into higher handling units.
Additionally, you can add or remove handling units from a delivery or build a new HU without using an existing one. If any extra material is picked and needs to be returned to the warehouse, this is helpful. Additionally, you can edit or change the weights of already-created HUs as well as print labels.
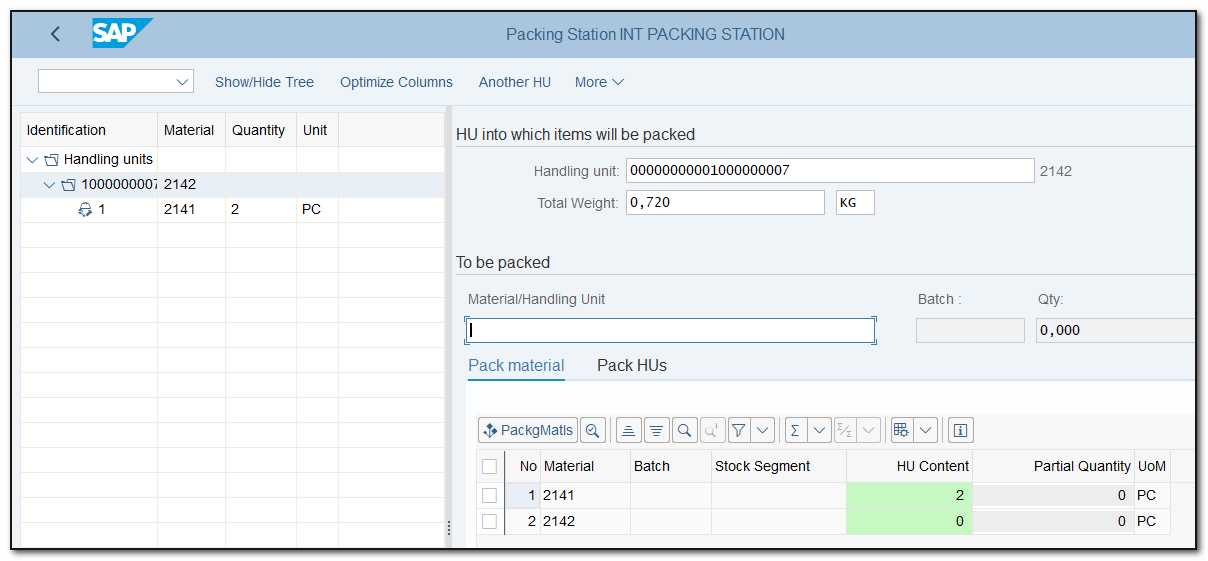
Figure 4 Packing station