The transaction code MM01 can be utilized to either create a new material master record or to extend an existing one. The menu can be accessed by following this path:
SAP Menu ➢ Logistics ➢ Sales and Distribution ➢ Master Data ➢ Products ➢ Material ➢ Other Material ➢ Create
You specify the material type that you intend to set up on the screen depicted in Figure 1. To identify the industry (Chemical, Pharmaceutical, Retail, and so on) to which the material belongs, use the Industry Sector field. To expand existing material, simply enter the material number and the system will automatically populate the industry and material type.
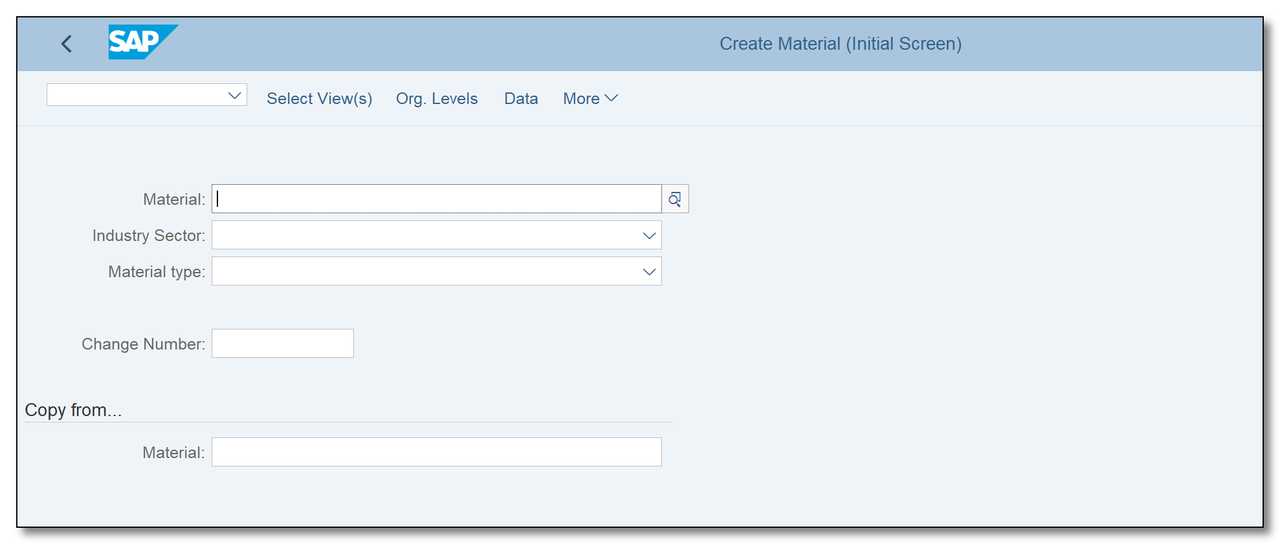
Figure 1 Material Creation – initial view
To use an existing record as a basis for a new product, the Copy From field can be used to select the appropriate source material and organizational level.
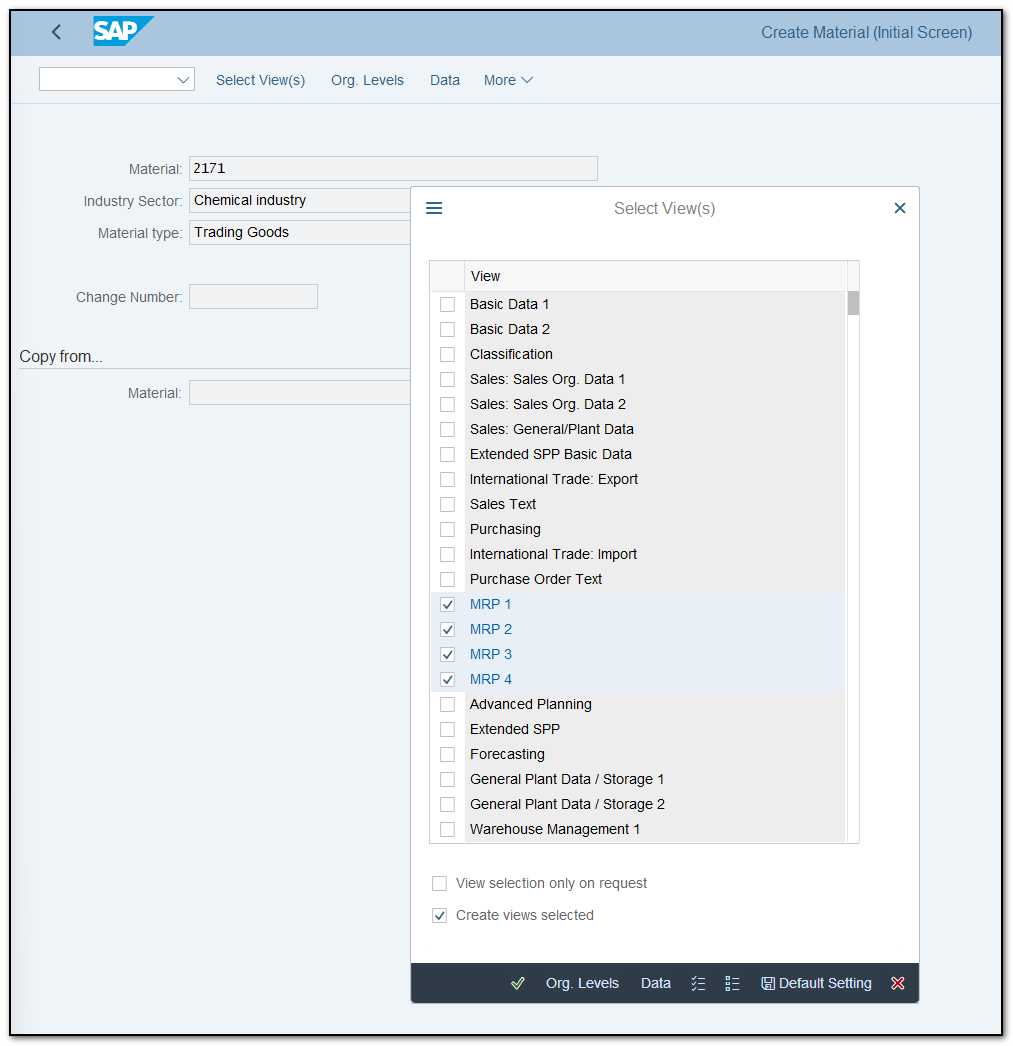
Figure 2 Material Creation - selecting views
You can select which data screens you want to build by clicking the Select View(s) button. For manufacturing department, choose the views as shown in Figure 2.
Once you select the views and press Enter, another dialog box will appear.
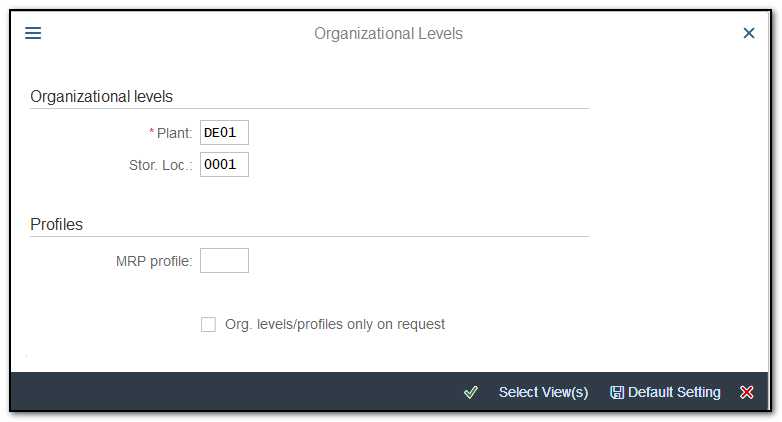
Figure 3 Material Creation – Organizational Levels Selection Window
You must next specify the organizational levels (plant, storage location) for which the data will be created based on your choice.
To view all values for the plant or storage location, where the selected material is already maintained, press either F4 or the Search button while in Change and Display transactions on the SAP system.
Once you confimr your choise you will be redirected to the first MRP view. Material Requirement Planning views contain data that is unique to a plant and a storage locations. The MRP type, controller, and plant-specific material status are among the MRP-related details contained in this data. The material master contains data that is pertinent to material needs planning (MRP) across four views. The names range from MRP1 through MRP4. Setting here has an impact on inventory management and material availability check.
MRP1 View
Planning type is the only field in MRP 1 View that is required. We'll go into greater detail about the key areas that are utilized in a productive setting.
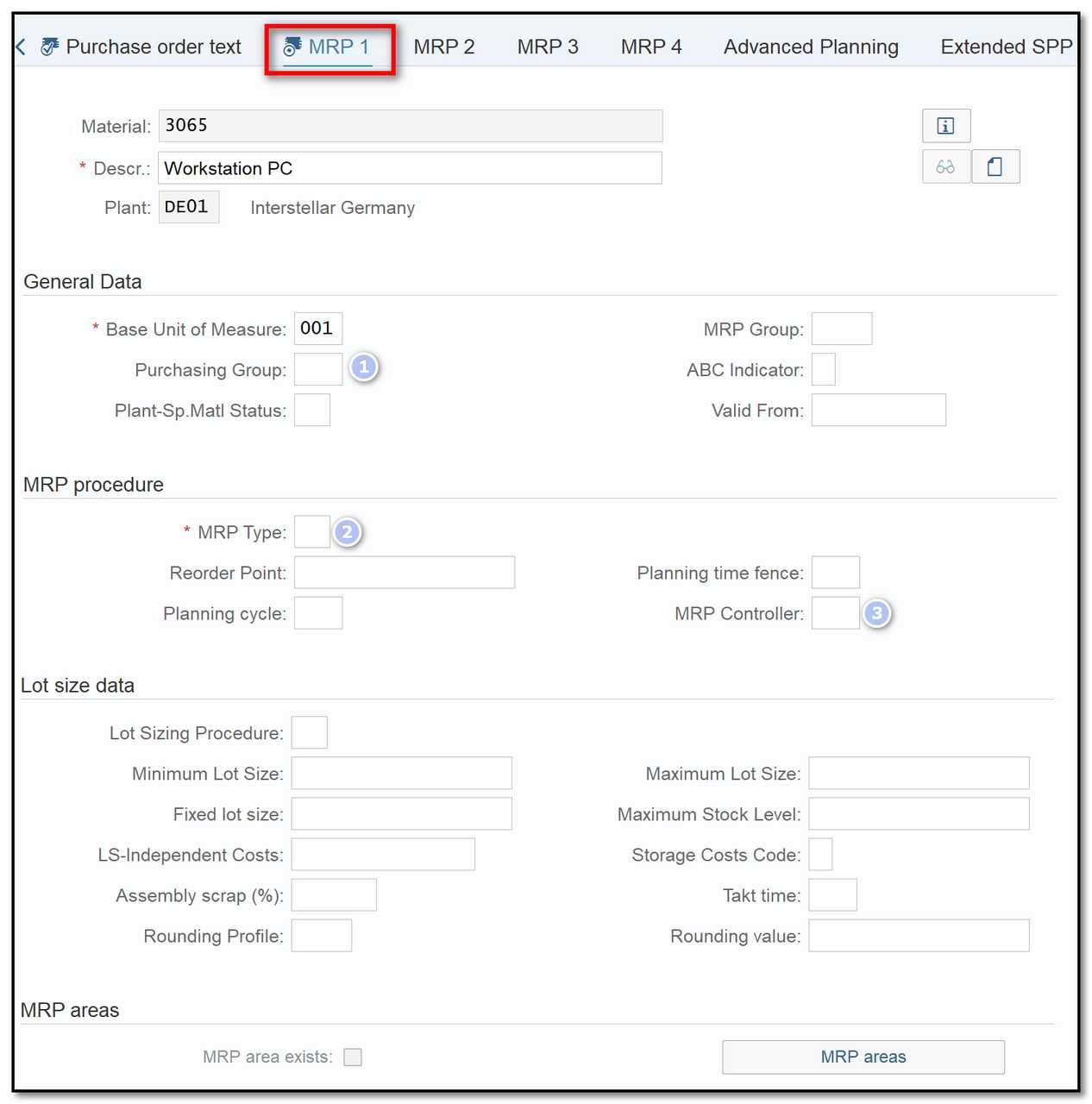
Figure 4 Material Creation – MRP1 View
Purchasing group (1) This option is used to specify the default purchasing group for this particular material.
MRP type (2) There are numerous MRP types that can be used. In this instance, our MRP controller indicated that PD, the default MRP for the majority of SAP installations, should be used.
MRP controller (3) The MRP controller in control of this material's production monitors all the data in these MRP views, as well as the MRP results themselves, production planning for this material, etc. The data for MRP views is typically provided by the MRP controller; in some organizational models, MRP controllers even maintain these views on their own.
MRP 2 View
Procurement, scheduling, and net needs calculation data are included in MRP view 2.
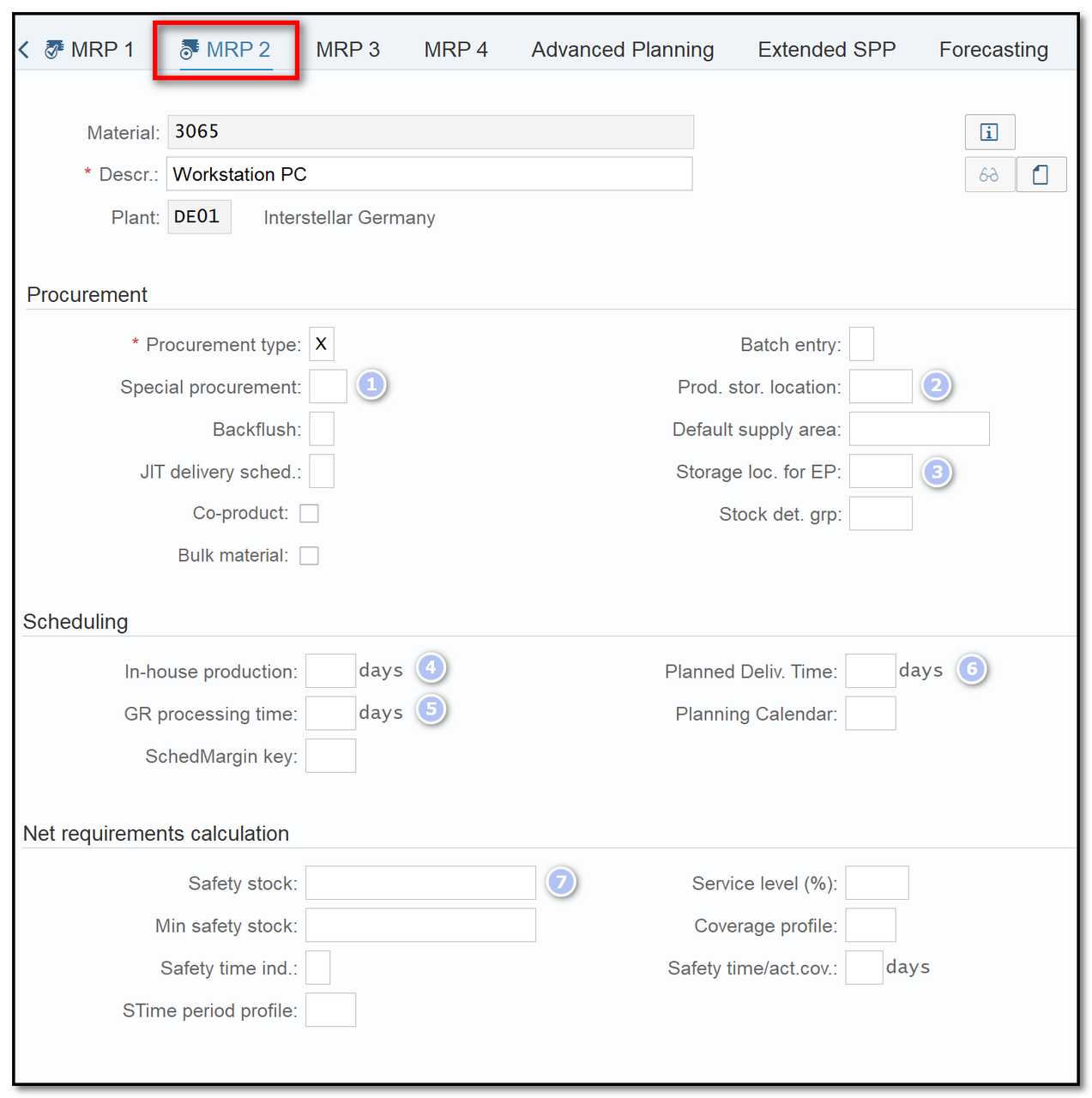
Figure 5 Material Creation – MRP2 View
Procurement type Here, you can select whether your material is produced internally (as in our case), externally, or if both forms of purchase are possible. Additionally, procurement might not exist at all.
Special Procurement (1) When you wish to be able to modify or override the procurement type defined in the material master, you utilize special procurement.
By designating the special procurement as external, you can still force the system to ignore the BOM and routing even if the procurement type is internal and treat the material as if it were obtained externally.
Production storage location (2) The storage location that is copied throughout the production documents will be maintained here. This indicates the place from which the products issue is posted if it is a production component, or if it is produced material, it indicates the location from which the material receipt is posted.
Default storage location for external procurement (3) Here, you can keep the storage location that was suggested in the purchase requisition for use in future material storage. When a material is purchased from outside sources, this storage location is suggested in the anticipated sequence in the materials planning.
In-house production time (4) Indicates how many workdays are required to produce the material internally. The order quantity has no bearing on the length of internal production.
Goods Receipt Processing Time in Days (5) This figure, which reflects the number of days required for the inspection and placement of the products in the proper storage location, can be set up.
Planned Delivery Time in Days (6) if the item or service is purchased externally, the number of calendar days required to receive it. When using many vendors for a single material, an average value must be specified. The same applies if you purchase the product from a set vendor with variable delivery dates.
Safety stock (7) specifies the quantity that will be used to meet an unexpected increase in business during the coverage period. The presence of a safety stock lowers the danger of deficits.
MRP 3 View
Several useful fields, primarily utilized by planning functions, are present in MRP view 3.
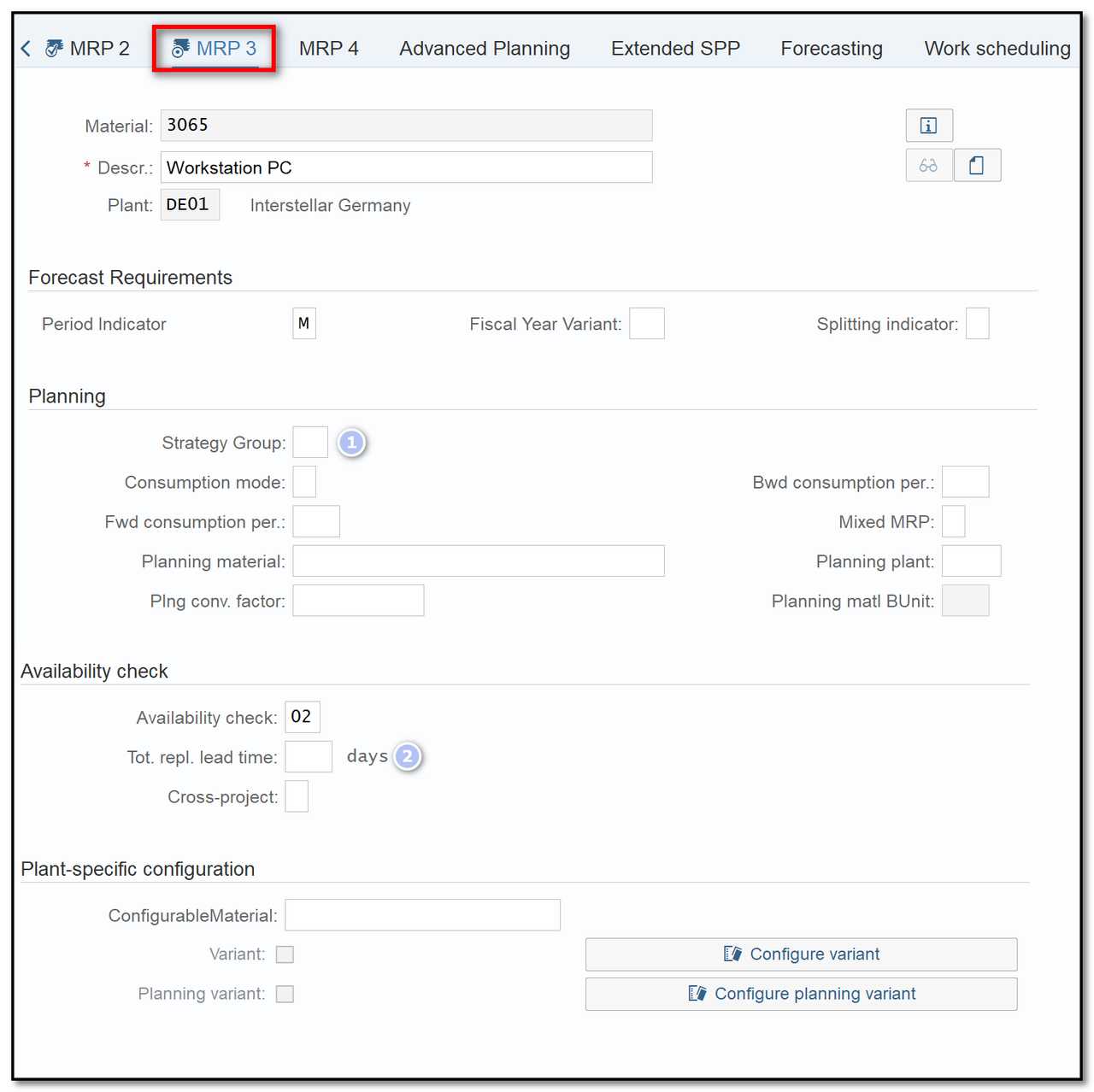
Figure 6 Material Creation – MRP3 View
Period indicator specifies whether material is to be scheduled or forecast daily, weekly, monthly, or annually. Most of the time, this is set to monthly.
Strategy group (1) For example, this can be configured to Make to Order, Make to Stock, etc., and is used to organize the planning strategies. The production planning management must decide which of the various solutions to use. The decision of which strategy group the material should be assigned is typically influenced by the material types and/or material ABC classification.
The total replenishment lead time (2) ) is the amount of time required after all BOM levels have been purchased or produced before the product is fully accessible once more. This field defines it as the sum of the internal production time(s) and/or projected delivery time(s) of the longest production path; it is not calculated by the system.
This period of time is required if the replenishment lead time for internally manufactured materials needs to be taken into account when determining availability.
MRP 4 View
This is the only MRP view that is kept up to date at the organizational level of plants and storage locations.
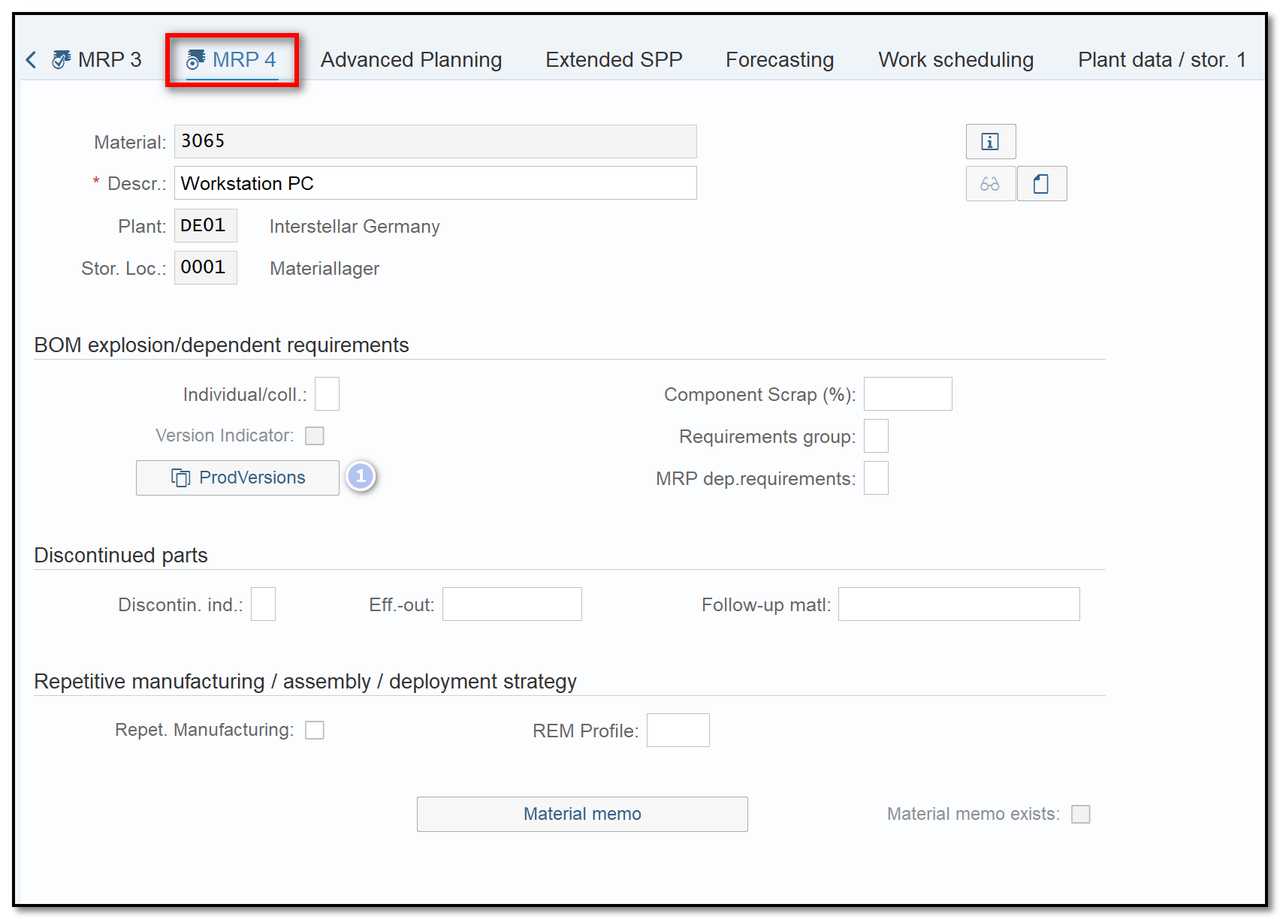
Figure 7 Material Creation – MRP4 View
Production Version a key that determines the several production methods that can be used to make a material.
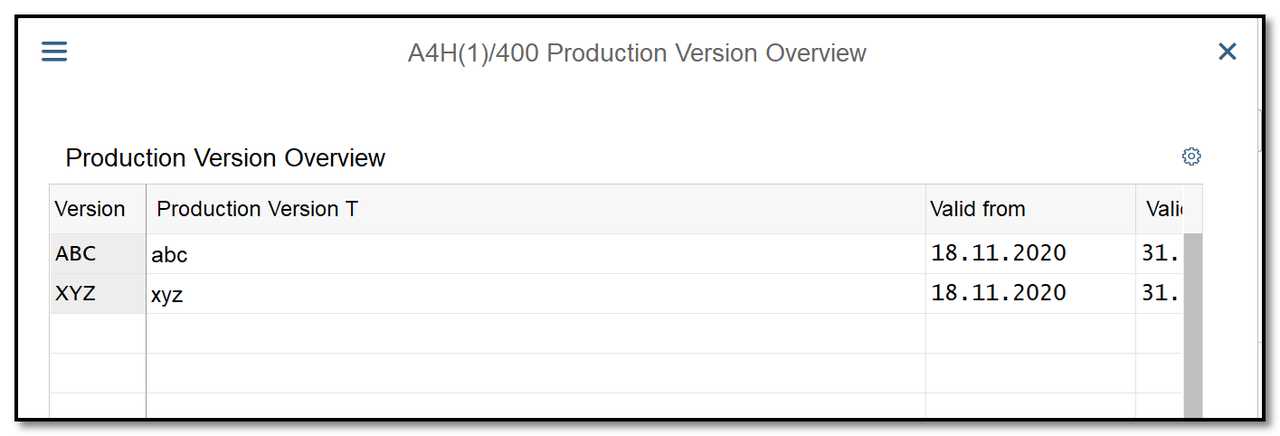
Figure 8 Material Creation – Production Version
The following is decided by the production version:
- BOM's substitute for a BOM explosion
- The lot-size constraints for repetitive production
- The task list group, the task list group counter, the task list type
Work Scheduling View
Production uses this view to manage the scheduling of production and handle orders. During a scheduling run, capacity requirements are estimated for all of the materials according to a production schedule. When handling material in batches, you can also turn on batch management here. Activating batch management is possible in a number of additional views.
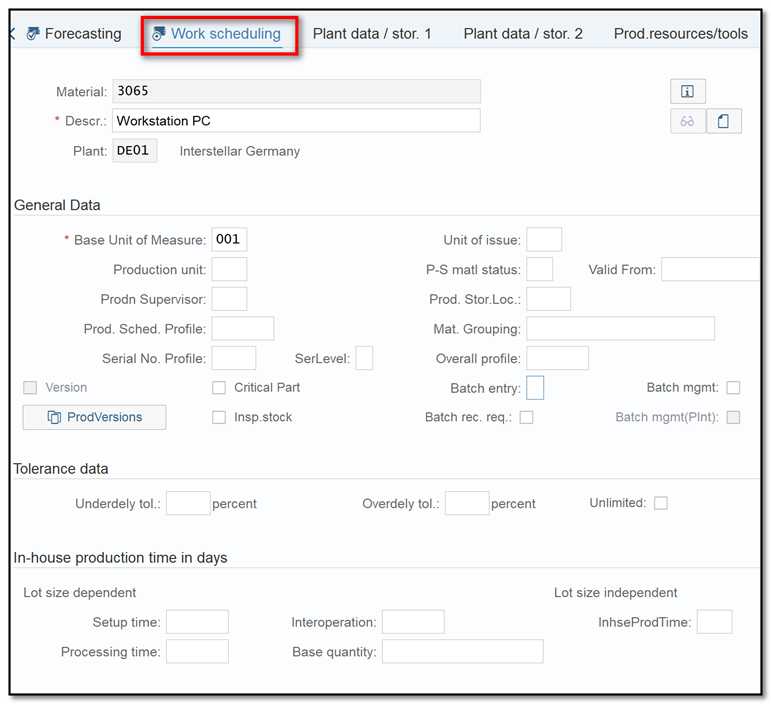
Figure 9 Material Creation – Work Scheduling View
Advanced Planning View
Advanced Planning View in SAP material master allows businesses to optimize the planning and management of their materials. It provides a comprehensive view of the entire supply chain, from the initial request for raw materials through to the end delivery of finished goods.
Figure 10 Material Creation – Advanced Planning View