SAP source determination helps buyers find the best vendor for their purchase requisition. The vendor account is the source of supply. Preferred vendors are listed as source lists in master data elements. When creating a requisition, SAP checks for a source list for each item if the source determination indicator is set in the header.
The SAP source list is a list of vendors for a specific plant and time period. Each material and plant combination has its own source list, which includes the vendor's preferred supply time and identifies if the source is fixed, blocked, or relevant to MRP. Before using the source list, we must fulfill certain prerequisites. Afterwards, we review the fields of the source list master record. Various methods exist for creating a source list, and we provide an example. Lastly, we show how the source list is utilized during purchase requisition creation.
SAP Source List Prerequisites
An SAP source list is a master data record that can be created by an authorized user at any time. Certain settings enforce the requirement to use a source list, such as making it mandatory at the plant level through configuration or requiring it at the material level through a material master data setting.
To ensure that all materials belonging to a specific plant have a corresponding source list record, it is necessary to define the source list requirements at the plant level. This can be done through transaction code OME5 or by following the customizing path:
Materials Management ➢ Purchasing ➢ Source List ➢ Define Source List Requirement at Plant Level
Search the plant that needs a source list to be maintained and mark the indicator in the Source list column. You can also mark indicator for other plants if necessary. For instance, in the given example, plant DE01 – Interstellar Germany 1 necessitates a vendor to be mentioned in a source list for the creation of a purchase order. Save the changes.
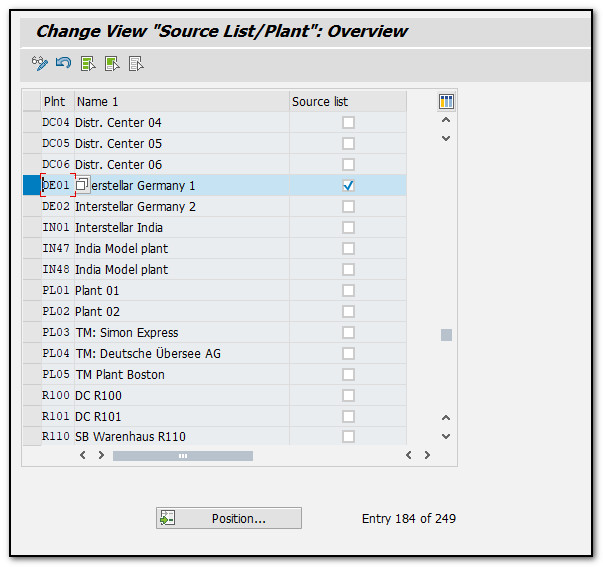
Figure 1 Source List Required at Plant Level
To require a source list for specific materials, skip the plant level configuration and set the source list requirement at the material level. This can be done by marking an indicator in the material master record, which will enforce a source list to be maintained before creating a purchase order for that material. To do this, go to transaction code MM02 and access the relevant materials in change mode. Then, go to the Purchasing tab and check the Source list indicator.
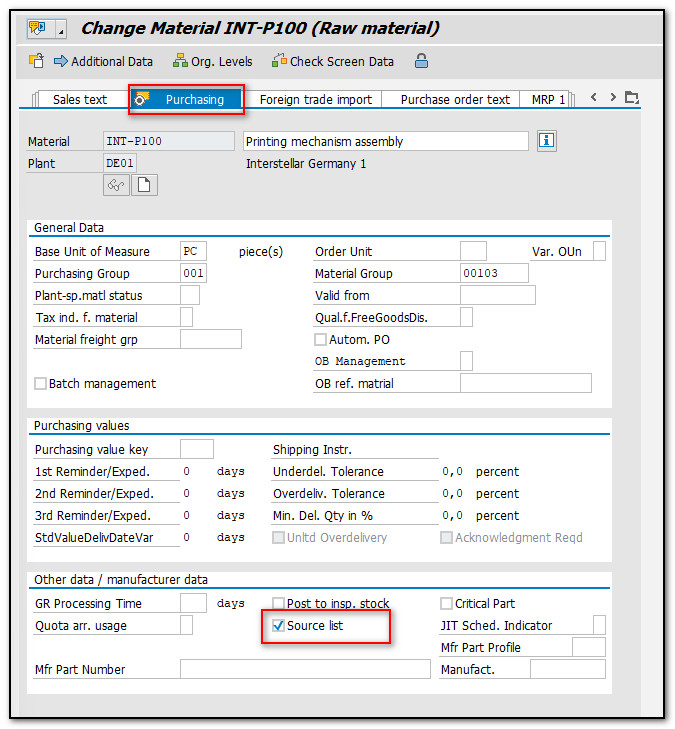
Figure 2 Source List Required at Material Level
SAP Source List Creation
A source list master record in SAP can be created in various ways, as explained in the following sections.
- Manual Creation
- Creation Within an Outline Agreement
- Creation Within a Purchasing Info Record
- Automatic Creation
Creating a source list record is useful when you want to create a new record or add to an existing one. For example, if a company needs to buy ethernet coaxial cables from an external vendor, they can create a source list for the material. This list will link the material to the supplier and be maintained by the employee in charge of purchase requisitions. Let's see the steps to manually create a source list for this situation. Go to transaction code ME01 or use the menu path:
Logistics ➢ Materials Management ➢ Purchasing ➢ Master Data ➢ Source List ➢ Maintain
In the initial screen of transaction code ME01, you enter the material number and plant. In the example below, the material number INT-P100 represents the printing mechanism assembly for which we are creating the source list.
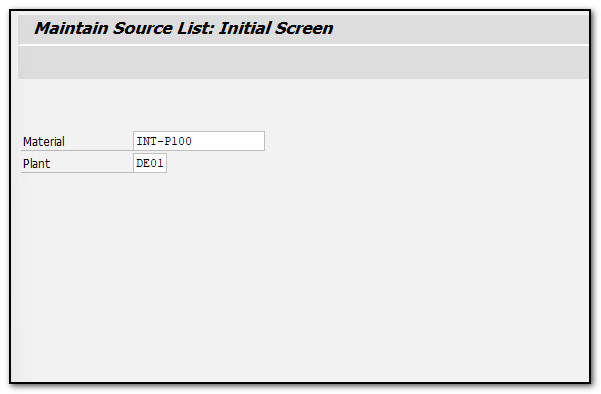
Figure 3 Create Source List Initial Screen
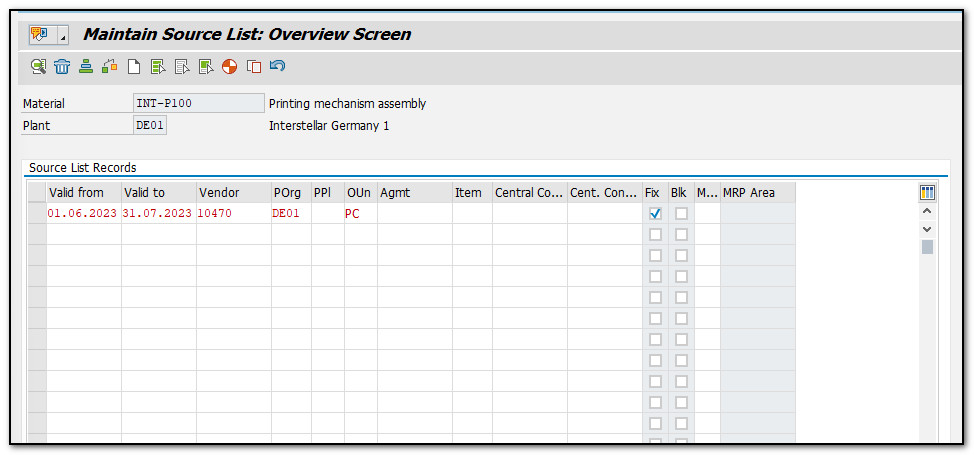
Figure 4 Create Source List Overview Screen
Now, let's discuss the fields of a source list master data record.
Valid from/Valid to: These fields contain the validity date range that specifies when a vendor will be the source of supply for the material and plant combination.
Vendor: Provide the master record number for the source of supply for the material.
POrg: The purchase organization and vendor number are required fields for maintenance.
PPl: If the material is sourced internally, the procurement plant number should be entered in this field. This field is only applicable for materials with stock transfer type.
OUn: The preferred unit of measure for orders from this source of supply is stored in this field.
Agmt: If there is an existing agreement with the vendor, enter it in this field.
Item: This field contains the item number from the outline agreement, if it is applicable.
Fix: The indicator should be set if the vendor is the preferred source of supply for the material and plant combination.
Blk: If a specific vendor is to be restricted from supplying the material for a designated period, then this indicator should be activated. It will prevent the creation of any purchase order or purchase requisition with that vendor.
MRP: This field is used to indicate the relevance of the material to material requirements planning.
In the maintain source list overview screen, enter the Valid from, Valid to, Vendor, POrg, OUn and other relevant fields as described in the previous section. Then, press Save to create the source list.
To create a source list for an item in the outline agreement, go to the outline agreement overview screen and select the item. Then, choose Item ➢ Maintain Source List from the menu bar.
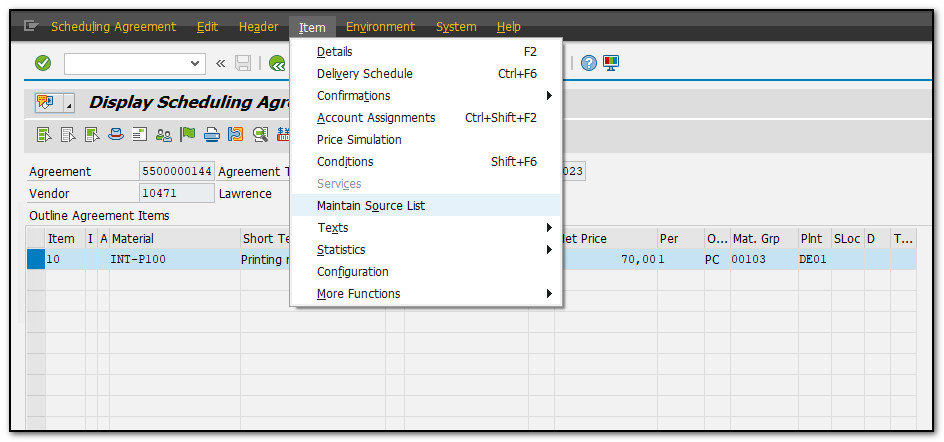
Figure 5 Source List Creation Within an Outline Agreement
Proceed with the source list creation as described in the previous section for manual creation.
A source list record can be maintained when creating or changing a purchasing info record. In the info record screen select Extras ➢ Source List from the menu bar.
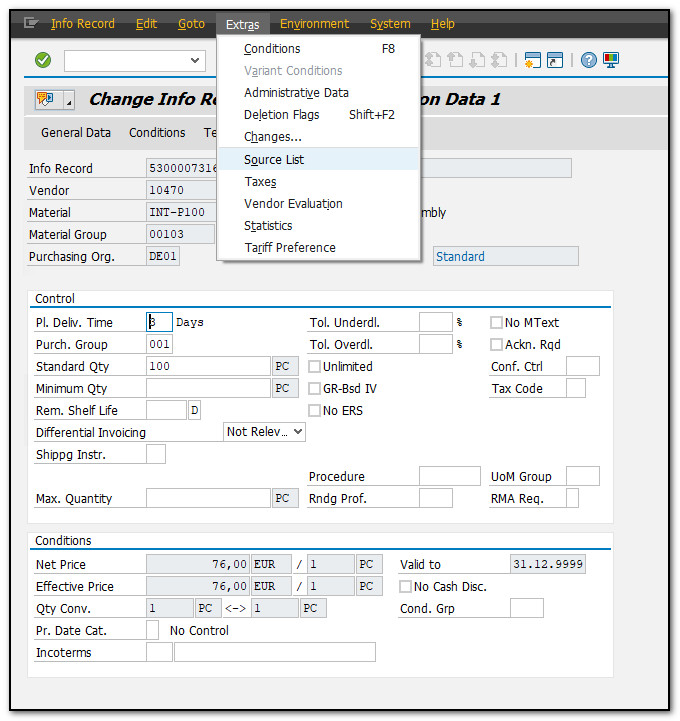
Figure 6 Source List Creation Within a Purchasing Info Record
Proceed with the source list creation as described in the previous section for manual creation.
Every information record or outline agreement can automatically generate a source list record, choosing for one or more materials. Go to transaction code ME05 or use the menu path:
Logistics ➢ Materials Management ➢ Purchasing ➢ Master Data ➢ Source List ➢ Follow-On Functions ➢Generate
Specify the material(s), plant(s), and date range for which to generate the source list in the transaction code ME05's start screen. To display the source lists that will be created, click Execute. Prior to real execution, this can be done in test mode.
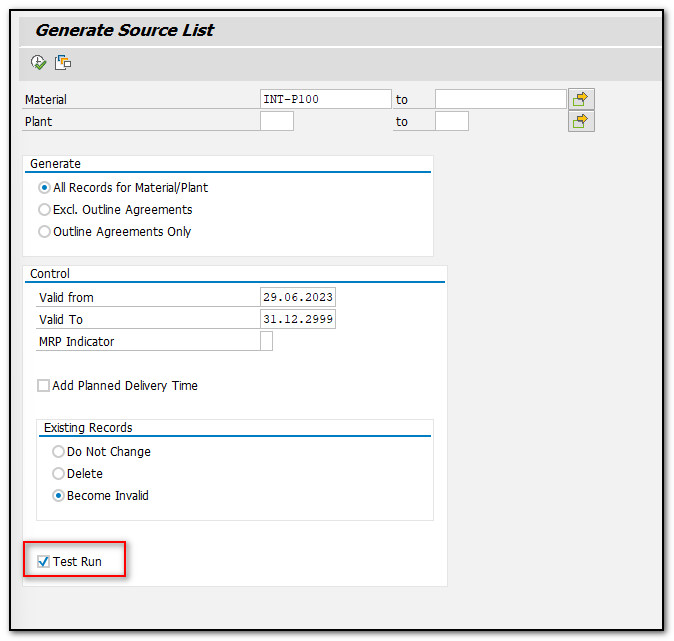
Figure 7 Generate Source List Initial Screen
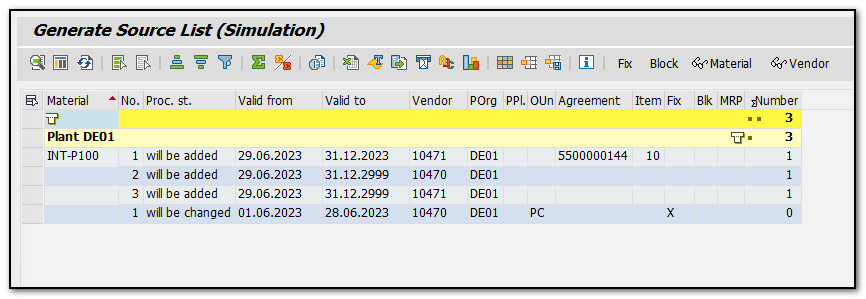
Figure 8 Generate Source List Simulation