1. Document Type
Standard document type used for stock transfer order is UB. If you need a custom document type, you can create a new using the menu below:
Menu Path
IMG ➢ Materials Management ➢ Purchasing ➢ Purchase Order ➢ Define Document Types
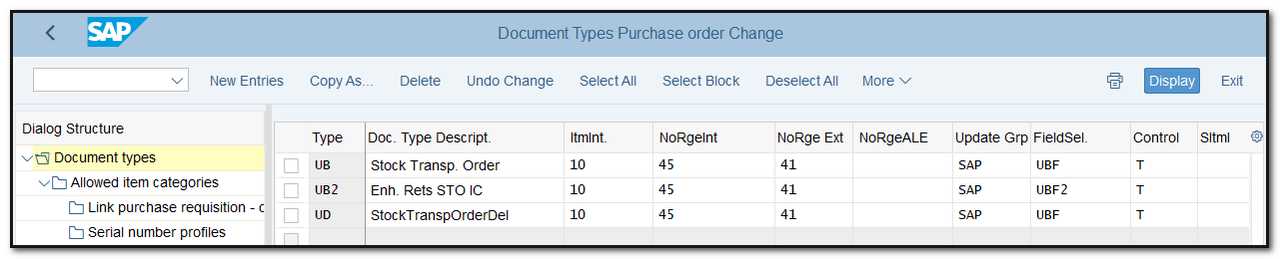
Figure 1 Document Type for Purchase orders screen
2. Shipping data
Shipping Data needs to be maintained for both supplying and receiving plant.
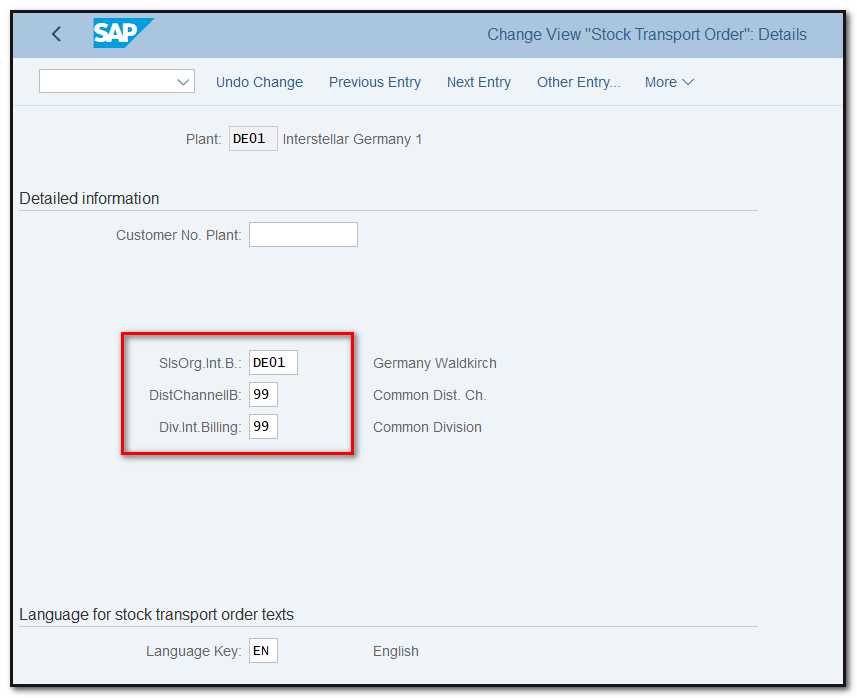
Figure 2 Shipping Data for supplying plant
Customer assignment to the receiving sales area is required during shipment data maintenance.
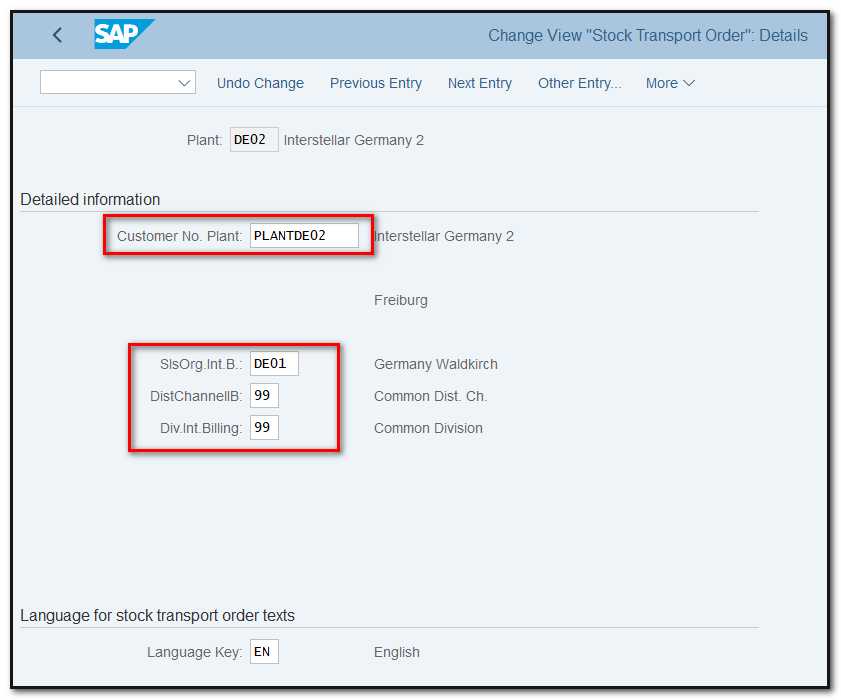
Figure 3 Shipping Data for receiving plant
3. Create and define checking rule
First create checking rule or use existing one and then define this checking rule in combination with Availability Check Group assigned in material master.
Menu Path:
IMG➢ Materials Management ➢ Purchasing ➢ Purchase Order ➢ Set up Stock Transport Order ➢ Create Checking Rule
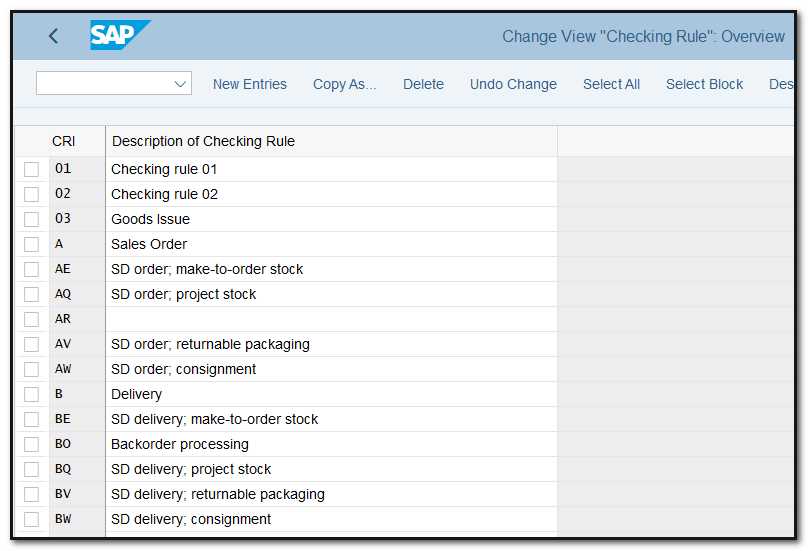
Figure 4 Checking Rule Creation, overview screen
Menu Path:
IMG➢ Materials Management ➢ Purchasing ➢ Purchase Order ➢ Set up Stock Transport Order ➢ Define Checking Rule
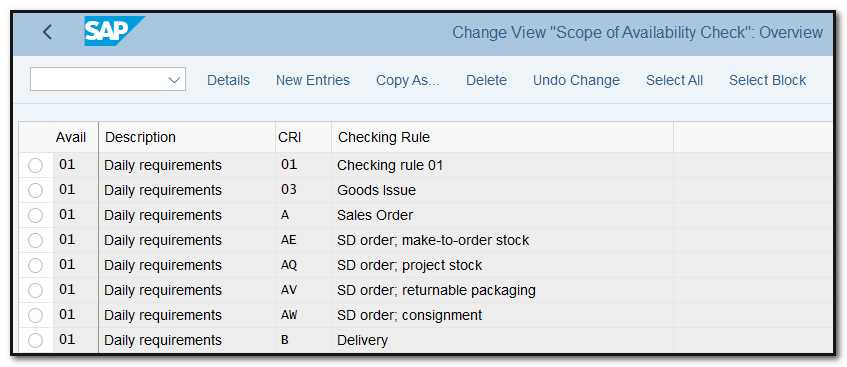
Figure 5 Checking Rule, scope of Availability Check
4. Configure Delivery Type Availability Check Procedure by Plant
Supplying plant need to be assigned to Delivery type “NL” and purchase document type “UB” and checking rule “B”.
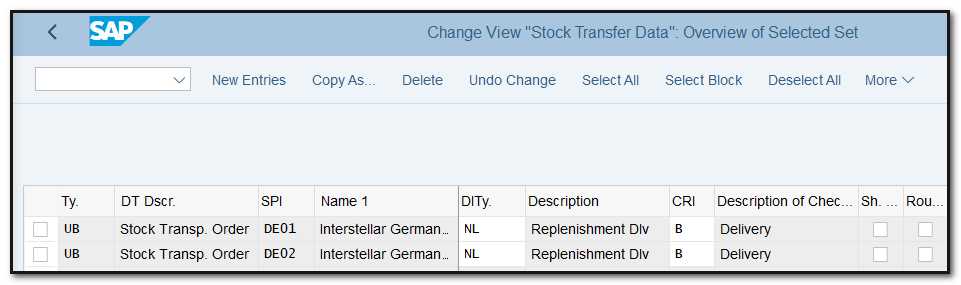
Figure 6 Delivery Type Availability Check Procedure by Plant, overview
5. Assign Document type, One step procedure, underdelivery Tolerance
The combination of supplying and receiving plants requires the assignment of purchasing document type "UB". If required enable a one-step process at the receiving and supplying plants combination.
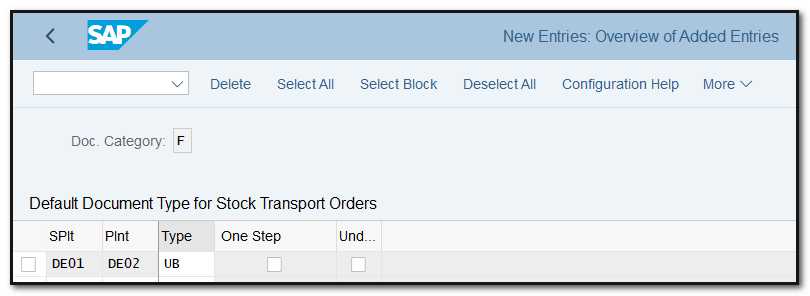
Figure 7 Assignment of Document type, One step procedure and underdelivery Tolerance\
6. Shipping Point Determination
Shipping point determination need to be done for both supplying and receiving plant.
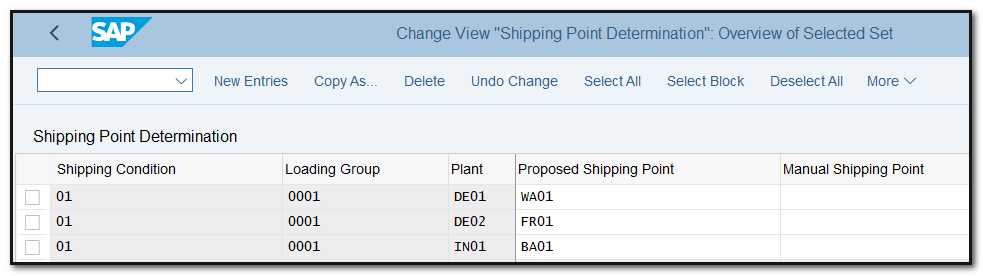
Figure 8 Shipping point determination